Overcoming the challenges of machining nickel-based alloys
As components made from nickel-based alloys become increasingly prevalent across the aerospace industry, demand for optimized cutting tools continues to grow. But, despite their advantages, nickel-based materials exhibit poor machineability due to their low thermal conductivity, potential for adhering to cutting tools and the presence of abrasive particles within the alloy structure. Due to these issues, productivity with carbide tools tends to be low. In addition, part complexity means that some components demand extended reach. Here, Henri Sevonen – Senior Industry Segment Manager – Aerospace for the metal cutting specialist Sandvik Coromant, explains how new ceramic end mill technology has emerged to help meet these requirements, with the potential to optimize the machining of aero-engine parts and provide significant competitive gains.
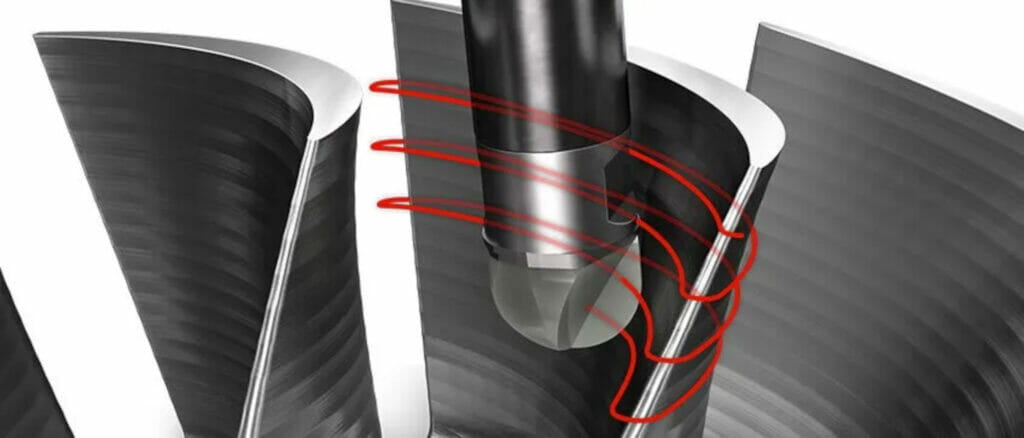
High temperatures arise when machining heat resistant super alloy (HRSA) materials.
Most aerospace parts are manufactured from heat resistant super alloys (HRSAs) and nickel-based alloys, which place a particular set of demands on production engineers looking to manufacture components like spools, turbine disks, combustion casings and blisks. Although many manufacturers use conventional solid-carbide end mills, such tools have their limitations in terms of performance when it comes to nickel-based alloys.
In a highly competitive global arena, aerospace machine shops are looking for next-level technologies that are capable of delivering a step-change in factors such as productivity and/or tool life. Ceramic end mills can provide that very leap, offering up to 20-30 times more machining speed, in comparison with solid-carbide tools for operations such as shoulder and face milling. Such impressive gains can be achieved largely because ceramic cutters retain their hardness at the high temperatures which arise when machining nickel-based alloys.
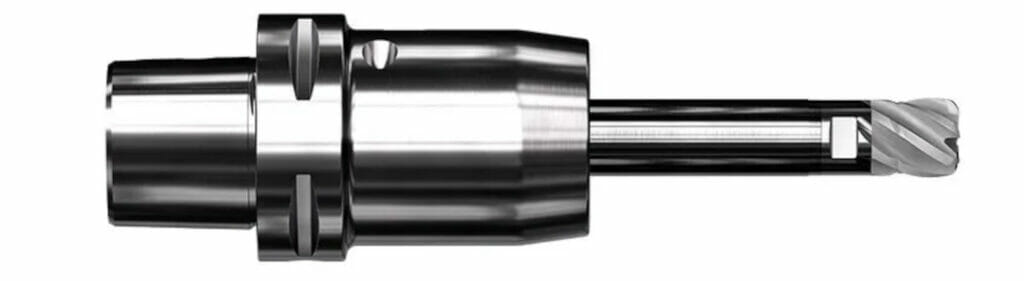
The brazed ceramic CoroMill 316 end mill is optimal for difficult reachability conditions, or to take advantage of the exchangeable head system flexibility.
The brazed ceramic CoroMill® 316 exchangeable-head end mill for roughing operations is a productive solution for aerospace engine applications in ISO S materials. In the first instance, the exchangeable head concept facilitates inherent process flexibility. Also available is a six-flute version with a straight corner radius that delivers highly productive side milling operations, and a four-flute version designed to boost face milling thanks to its high-feed face geometry.
The ceramic substrate of the end mills allows for a different cutting process in comparison with traditional solid-carbide tools. Importantly, the unique S1KU SiAlON grade is purpose-designed for the superior machining of nickel alloys, and is supported by negative geometry that provides a tough cutting edge. The latter also features a T-land for stable operations.
SiAlON carries a chemical composition of aluminium oxide and silicon nitride (Al203+Si3N4), a combination that promotes high wear resistance, even at elevated temperatures.
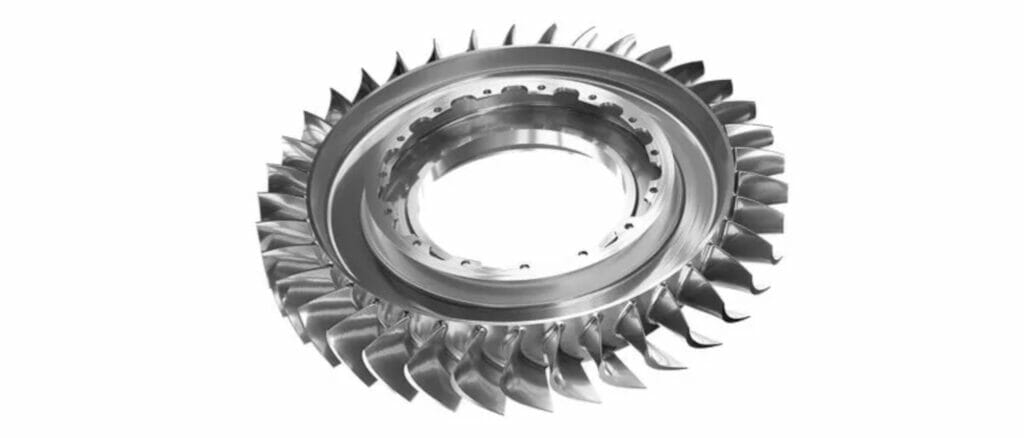
— Ceramic end mills retain their hardness at the high temperatures, making them especially suitable for blade machining of aerospace blisks.
Stable machining
A stable set-up is advised in all cases, and always without coolant application; machine shops should use pressurized air instead as coolant would simply burn at the high temperatures involved. In addition, the use of coolant promotes thermal shocks and has a negative effect on tool life. Importantly, high spindle speeds are required, of at least 13000 rpm. Further recommendations include the use of down milling, as well as a programmed tool path that keeps the tool in constant contact with the material.
It is clear that nickel-based alloys will play a vital role in the future of aerospace manufacturing. However, there are many challenges facing those tasked with producing aerospace engine components. It’s only through continued tooling innovations, such as ceramic end mill technology, that aerospace machine shops will be able to optimize the machining process.
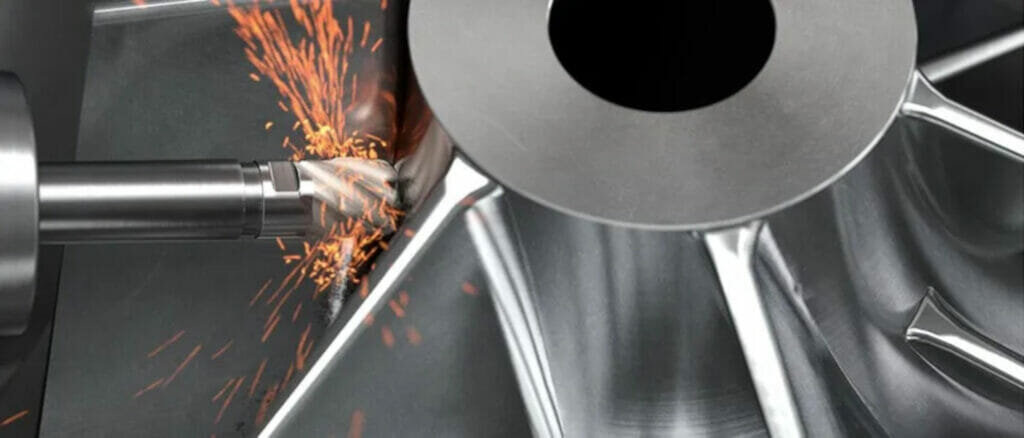
The CoroMill 316 Ceramic ball nose end mill has a brazed ceramic on carbide interface, which provides both strength and flexibility, and the ball nose geometry ensures an easier, faster profiling.
CoroMill® 316 is part of Sandvik Coromant’s optimized solid round tools range, visit the website for more information. Or, visit Sandvik Coromant’s aero engine applications knowledge resource aeroknowledge.com.
Sandvik Coromant
Part of global industrial engineering group Sandvik, Sandvik Coromant is at the forefront of manufacturing tools, machining solutions and knowledge that drive industry standards and innovations demanded by the metalworking industry now and into the next industrial era. Educational support, extensive R&D investment and strong customer partnerships ensure the development of machining technologies that change, lead and drive the future of manufacturing. Sandvik Coromant owns over 1700 patents worldwide, employs over 7,700 staff, and is represented in 150 countries.
For more information visit www.sandvik.coromant.com or join the conversation on social media.