Dynamic Load Monitoring (UK) Ltd. (DLM) has expanded its machine shop in Vancouver Wharf, Southampton and increased staff numbers, to meet demand for load pins.
A state-of-the-art suite of machining and milling equipment already gave DLM full control of its manufacturing processes, reducing lead times, but a newly installed Doosan Puma 3100LY computer numerical control (CNC) lathe will further boost capacity. It joins an existing lathe and a mill, in addition to a band saw and other CNC equipment shared with a sister business. DLM now employs three machinists, two operating lathes and another working with the mill. A technical manager and technical director oversee operations.
DLM has supplied load cells plus load monitoring and cable working equipment to the lifting, rigging, wind energy, and wider renewables sector for a decade. Previously, DLM would source the raw material — typically 17-4PH stainless steel — and outsource to a machinist that would machine the load cell billet according to drawings produced by the in-house design team. DLM would then complete strain gauging, assembly, proof load testing, and calibration.
Martin Halford, managing director at DLM, said: “A lot has happened in the year since we moved into the new [machine] shop. We had planned future expansion to gain more capacity and to be able to increase the size of the load pins we can manufacture, but the opportunity came up to purchase this machine ahead of time. We have seen an upturn in the number of custom load pins we have been manufacturing and expanded CNC capacity will empower us even further.”
DLM’s load pins are typically custom designed to meet clients’ specific physical size requirements. The new lathe enables DLM to machine larger pins, both in length and diameter; the product also has a Y-axis, enabling the machining of more detail, which wasn’t possible with the other lathe. The addition effectively doubles machining capacity.
Halford added: “While our [load] pin orders come from a myriad of sectors, we are seeing an ongoing uptick in demand from offshore industries. Speed is critical when dealing with the offshore market, as increased time often means huge increases in costs when a ship is not able to operate. Larger capacity gives us more scope to better handle bigger batches in-house and gives us full control over our supply chain as we approach the point where we are a fully vertically integrated operation.”
The machine shop expansion chimes with the company joining the Joint Supply Chain Accreditation Register (JOSCAR), which means it is approved to work on aerospace, defence, and security contracts, such as those overseen by the UK’s Ministry of Defence (MOD) and its supply chain partners. It is also a member of Make UK Defence, which champions the UK’s innovative and diverse defence and security manufacturers, along with the world-class supply chain that underpins them.
DLM’s Halford also confirmed plans for investment in testing capability at its calibration workshop.
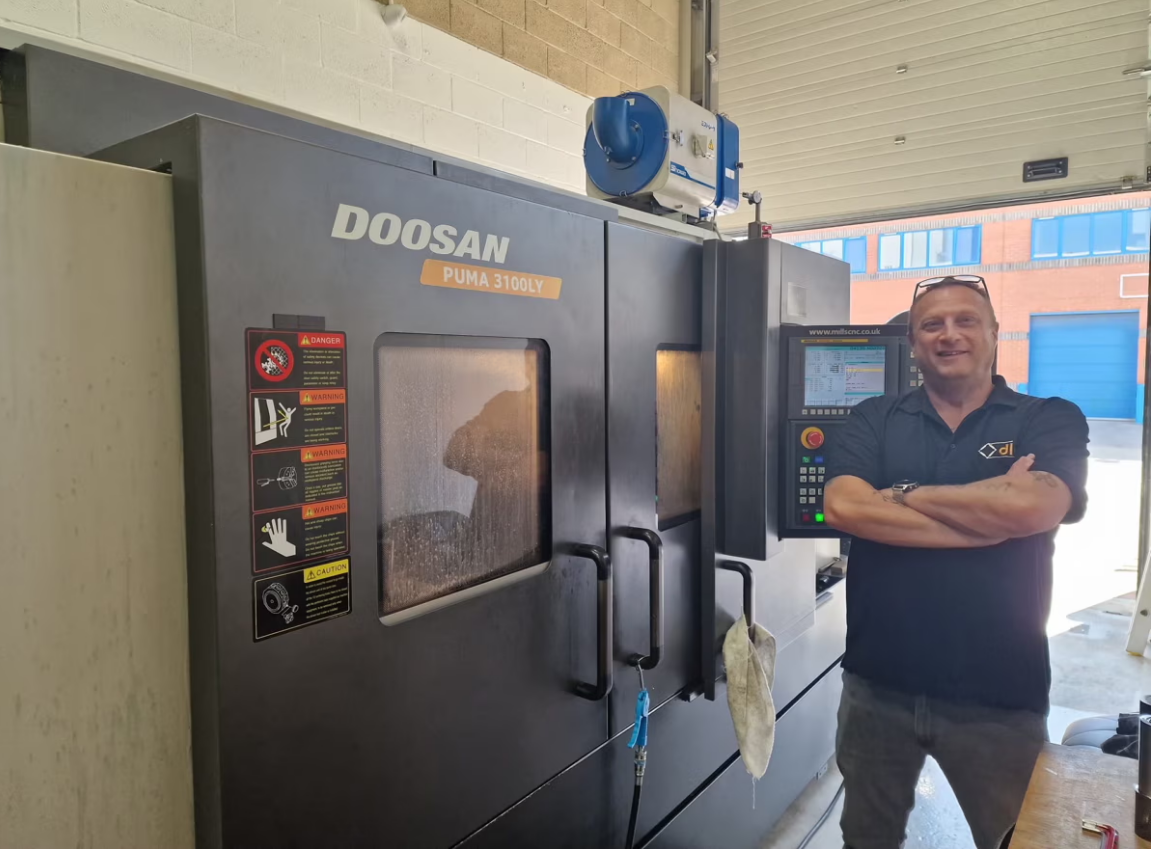
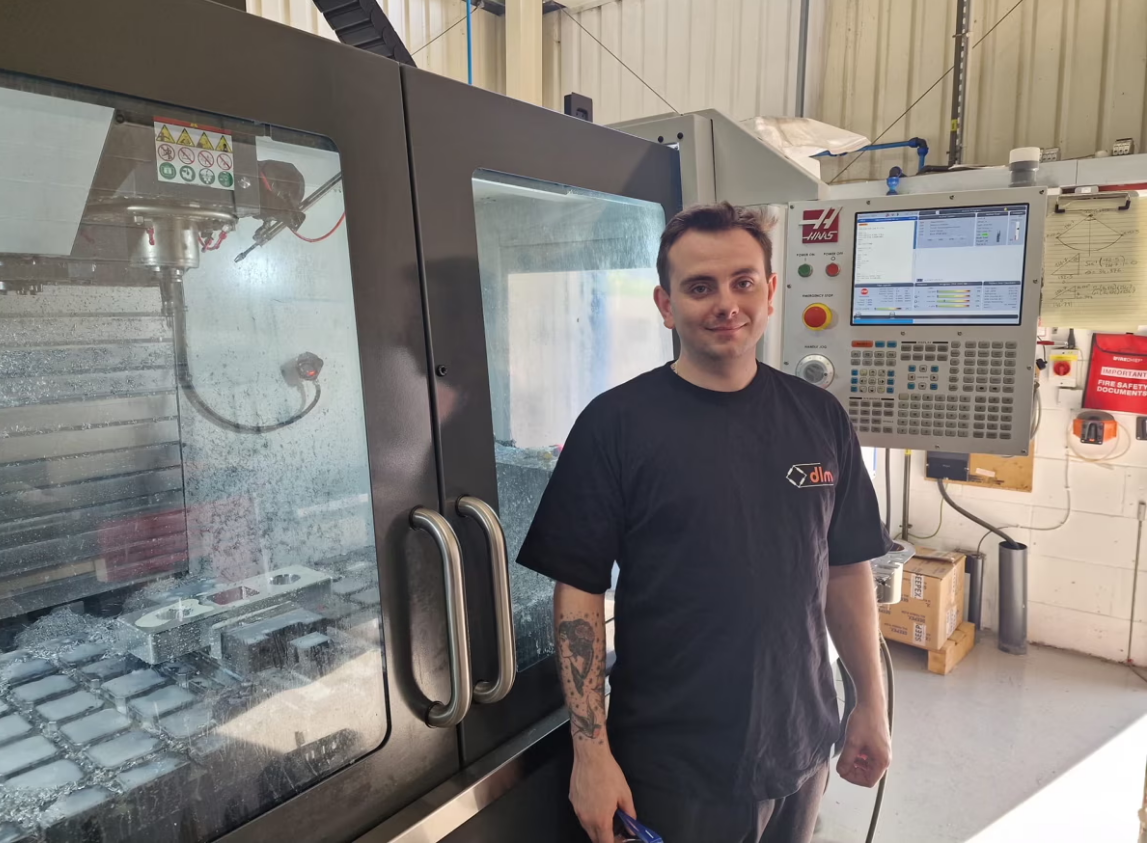
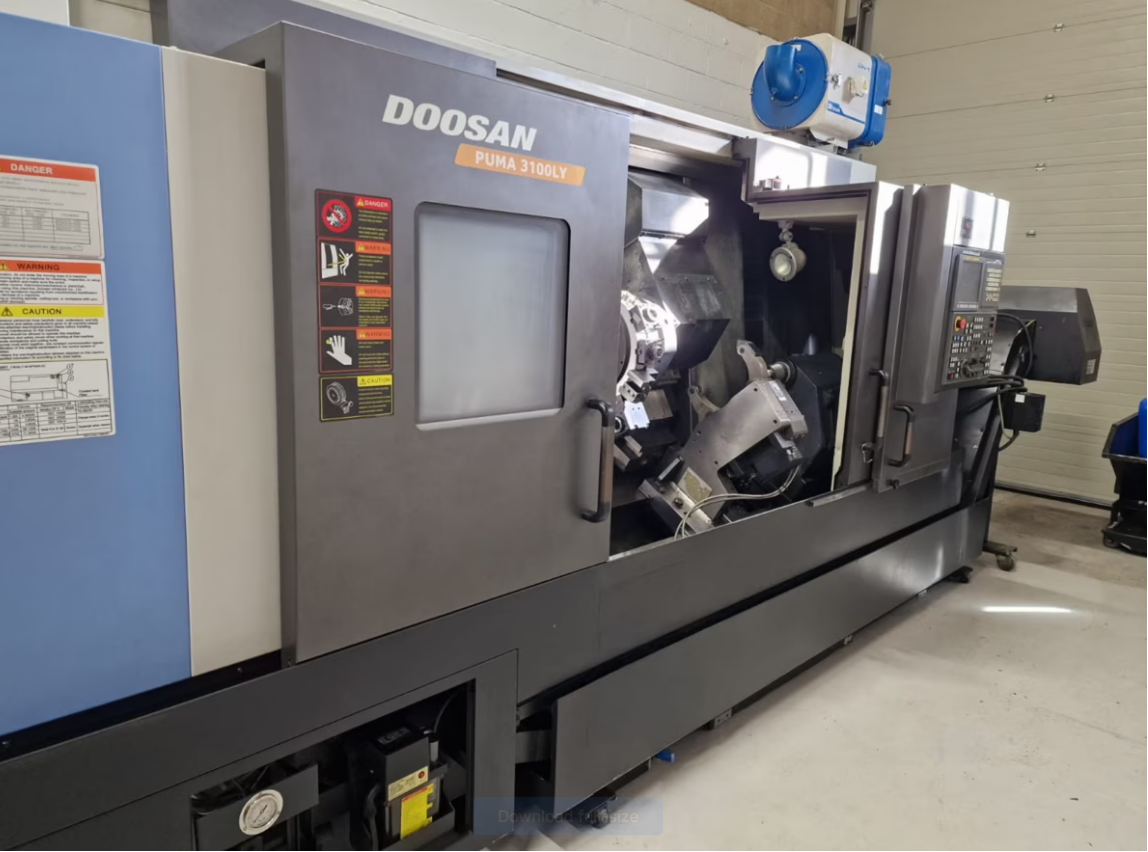