Eindhoven, The Netherlands (February 2025) — Alloys are indispensable in modern engineering due to their strength, durability and light weight. For quality assurance and performance optimisation, understanding the exact material composition of these alloys is key. Scanning electron microscopy (SEM) and energy-dispersive spectroscopy (EDS) have long been used to characterise materials, but traditional workflows can face challenges with complex alloys comprising of multiple materials due to their intricate microstructures. Here, Thermo Fisher Scientific explores these challenges and highlights how advanced solutions can help to accelerate material analysis.
Complex alloys have become ubiquitous in aerospace and manufacturing applications because their combined properties exceed those of their individual base metals. They offer several advantages over more conventional materials, with distinct use cases across a range of industries including aerospace, automotive and renewable energy.
For example, titanium alloys are widely used in aerospace structures due to their exceptional strength-to-weight ratio, corrosion resistance, and high-temperature performance. These alloys contribute to reducing aircraft weight and fuel consumption, ultimately lowering operational costs and carbon emissions. Their durability also makes them ideal for critical structural components, landing gear, and engine parts.
Meanwhile, aluminium-lithium alloys are increasingly employed in aerospace applications, offering high strength, reduced density and excellent fatigue resistance. Additionally, the corrosion resistance of nickel-based superalloys extends the lifespan of components exposed to extreme temperatures and harsh environments, such as jet engines and turbine blades. As the aerospace industry continues to prioritize lightweight, high-performance materials, the demand for advanced alloys is expected to grow to approximately $3.47 billion by 2030, driving innovation in material development and analysis.
Composition challenges
Despite their benefits, aerospace alloys present unique challenges in quality assurance, particularly in determining their precise composition. Since complex alloys and alloys in general consist of multiple elements and often multiple phases, a correct estimation of their varying distribution and an overall accurate characterisation can become complex.
Traditional SEM workflows often fall short when analysing such materials. Backscattered electron (BSE) imaging — which highlights differences in atomic weight — provides inconclusive results when materials have similar atomic weights or complex chemistries.
Additionally, conventional workflows can also fail to offer a complete picture due to overlapping spectral peaks or weak signal intensity. As a result, multiple analyses are often required, increasing time, costs and the likelihood of user error. In highly regulated industries like aerospace and automotive, where safety and precision are vital, incomplete or inaccurate material analysis can compromise product performance and lead to non-compliance with industry standards.
So, how can quality control and assurance teams gain a deeper understanding of alloys composition?
Addressing analysis issues
Advanced materials require equally advanced microscopy solutions. To overcome the limitations of traditional SEM workflows techniques, Thermo Fisher has developed ChemiPhase, a new component of ChemiSEM Technology. ChemiPhase is an automated and comprehensive feature designed to provide real-time material insights. It utilizes an advanced statistical engine to identify all chemically unique regions within the material of interest, ensuring thorough and precise analysis.
ChemiPhase identifies all statistically significant spectra within a sample, ensuring comprehensive characterisation without user bias. The software provides pixel-by-pixel phase maps, showing the distribution of unique phases with excellent clarity. Its automated detection capabilities require minimal user input, making the process faster and less prone to error.
Take for instance, the analysis of an additively manufactured Ti-6Al-4V alloy, a widely used titanium alloy that offers high strength and excellent resistance to corrosion and fatigue. The metal is rapidly and briefly melted with a laser during the additive manufacturing process, resulting in a completely new structure that often has complex variations in composition.
Since Ti-6Al-4V is frequently used within critical applications where failure would likely have severe consequences — such as engine components and orthopaedic implants (such as joint replacements, bone plates and screws) — identifying these compositional variations is crucial. However, traditional EDS analysis would not provide a complete understanding of the phases distribution. It is also likely that the operator would require a high degree of expertise to interpret the results.
ChemiPhase simplifies the process, automatically identifying alpha-Ti and beta-Ti phases and providing their composition and area fraction and in a single analysis. Correctly identifying these phases is crucial due to the impact they have on the strength, ductility and formability of the alloy.
ChemiPhase also offers significant time-saving benefits for quality assurance engineers. Even in the case of complex phase maps, ChemiPhase completes most acquisitions in less than one minute. This means that regardless of operator expertise, it is possible to generate rapid, accurate and reproducible results. Minor and trace elements are detected with precision, ensuring comprehensive insights into material composition.
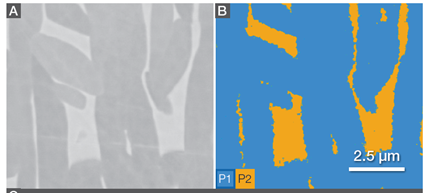
ChemiPhase Software easily maps the composition of a Ti-6AI-4V alloy (sample courtesy of GKN Aerospace Global Technology Centre, Bristol)
As industries increasingly adopt advanced alloys for their superior mechanical and physical properties, the need for precise material composition analysis becomes critical. While effective for simpler materials, traditional SEM workflows often struggle to accurately analyze the complex microstructures of aerospace alloys.
Reduced user bias, automated phase identification and reliable comprehensive insights all help to thoroughly study the material. ChemiPhase enables engineers to ensure the quality, safety and performance of their products.
To discover how ChemiPhase Analysis Software could streamline your material analysis processes for complex alloys, get in touch with Sales Account Manager (Electron Microscopy) Robbie O’Connell.