AM Solutions — 3D post-processing technology, a part of the Rösler Group, comes to this year’s Rapid TCT event drawing on an over 80-year history providing finishing solutions to industry, and a reputation for providing robust automated post-processing solutions to the additive manufacturing (AM) sector.
On booth 1229, visitors will be able to discuss their post-processing needs with AM Solutions’ expert team, and see a number of the company’s array of automated post-processing technologies which can finish parts from any AM process and in any material.
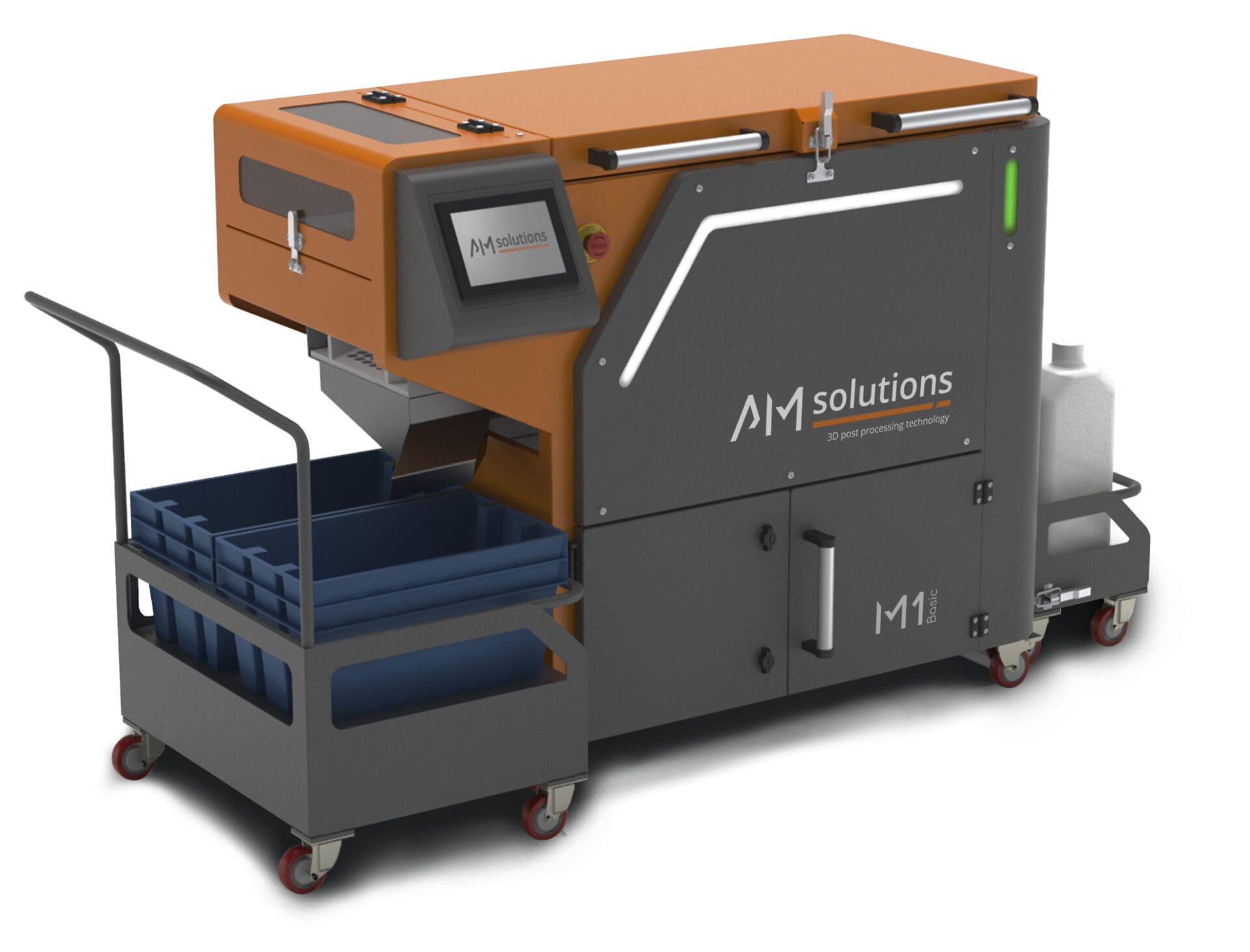
The M1 Basic — promoting superior surface finish of metal or plastic AM parts in a cost-effective and repeatable fashion, resulting in a flawless finish that enhances both aesthetics and functionality.
Tayfun Sigirtmac, CEO at Rösler / AM Solutions USA says, “Automated post-processing solutions are vital in AM because they streamline and standardise the finishing process, significantly reducing labour costs, time, and the potential for human error. These solutions ensure consistent, high-quality results by automating repetitive tasks such as cleaning and surface finishing. This not only enhances the efficiency and scalability of AM production but also improves the overall reliability and performance of the final parts. As AM adoption grows, automated post-processing becomes essential for meeting the increasing demand for precision, speed, and cost-effectiveness in the industry, and at AM Solutions we are meeting all these challenges and supporting AM as the manufacturing process of the future.”
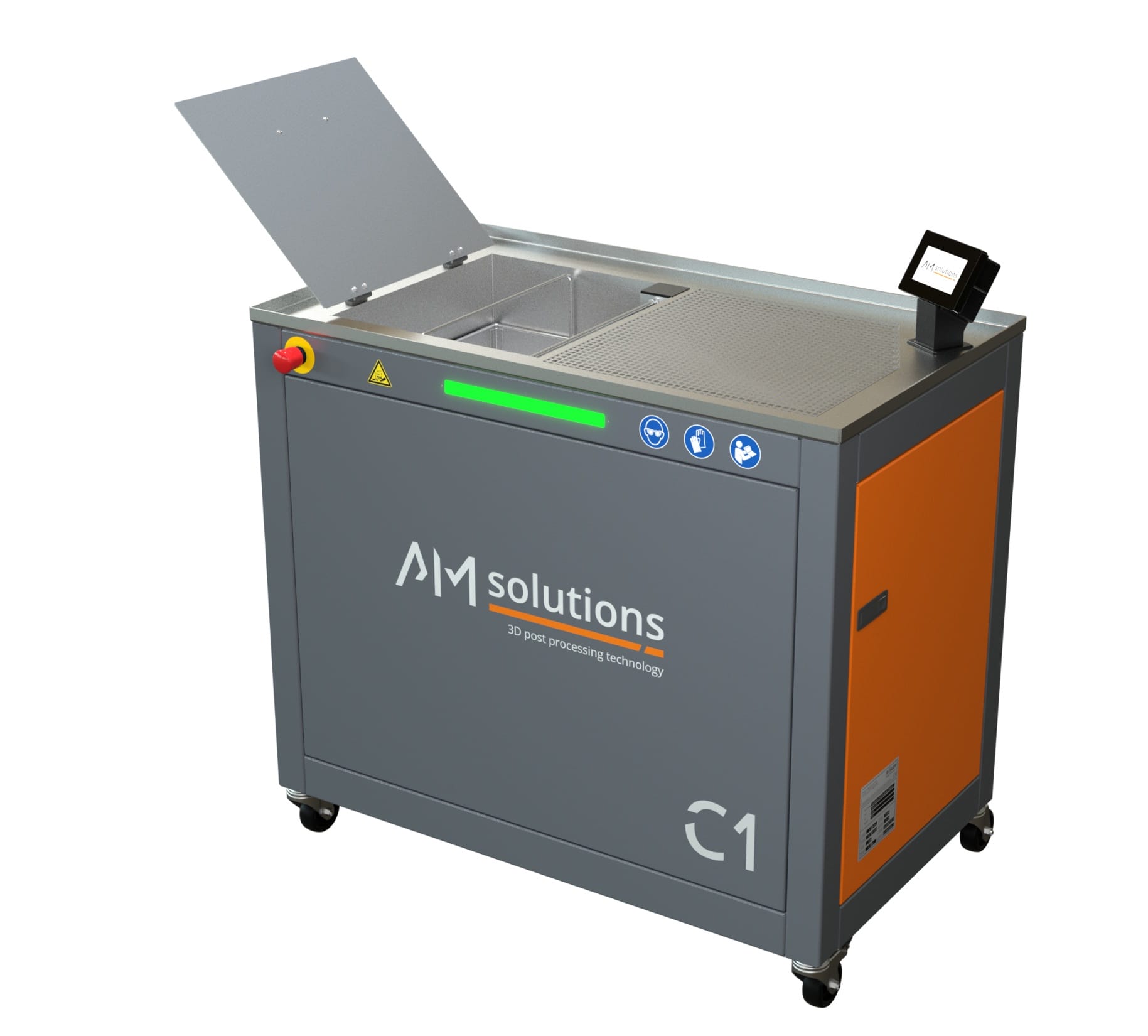
The C1 — an excellent tool for the automated and cost-efficient post processing of photopolymer components.
AM Solutions’ success builds on Rösler’s extensive surface finishing experience, and also on its innovation and customer-oriented process development in the field of AM, which means that processes are adapted to individual workpieces and process stage. As well as being vertically integrated and producing its post-processing machines in-house, AM Solutions also provides the consumables, which have been specifically developed with the unique characteristics of AM in mind. This combined expertise means that technology and consumables can be chosen to optimise the post-processing of any AM part. Coupled with a global after sales support network, AM Solutions is truly a product development partner for customer AM projects.
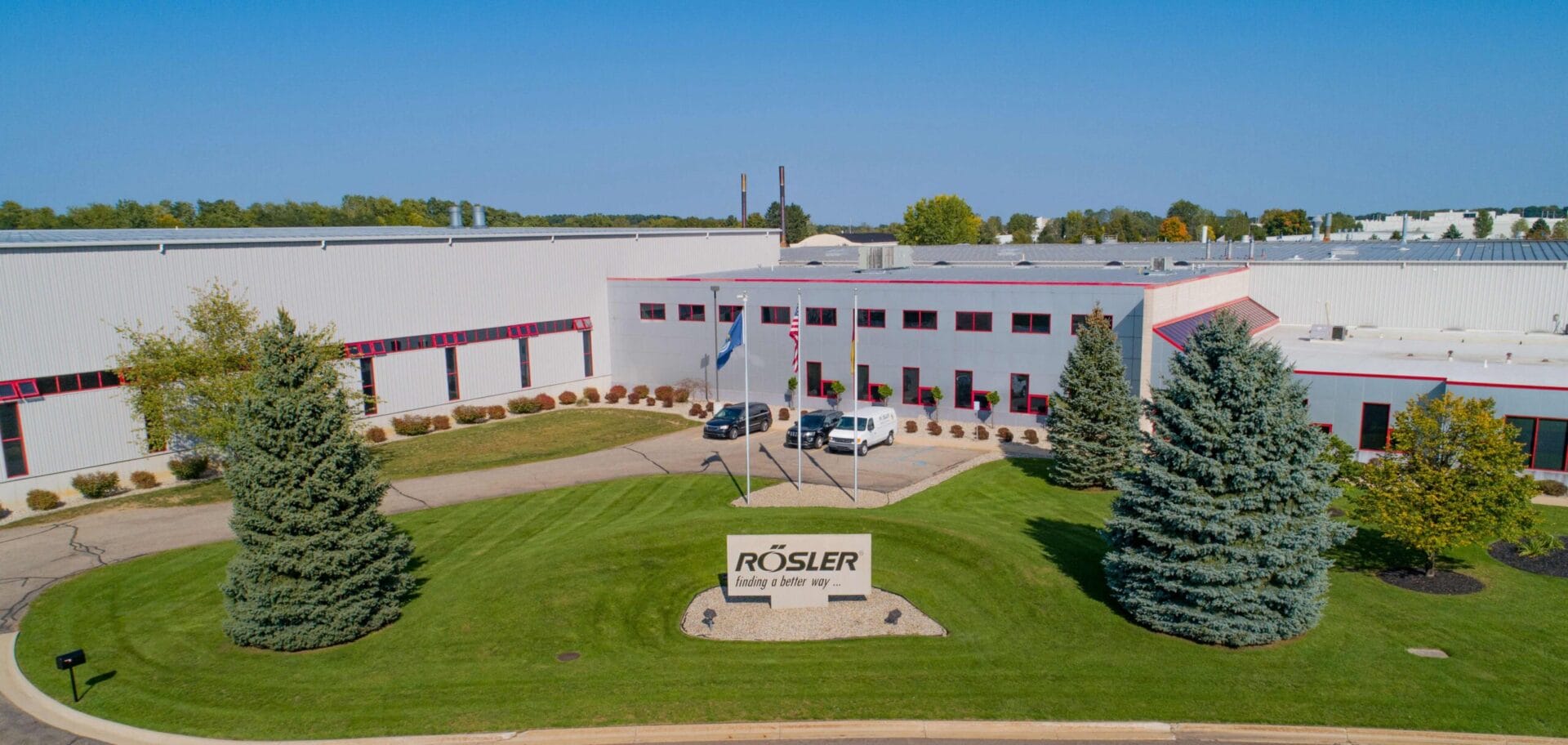
The United States-based branch of Rösler is headquartered in Battle Creek, Mich. The 300,000 sq. ft. facility houses manufacturing, warehousing, and production space as well as customer experience centers and training facilities capable of meeting and exceeding customer needs.
Sigirtmac continues, “At Rapid-TCT AM Solutions will be proudly exhibiting its S1, S1 Wet, M1 Basic, and C1 machines. The S1 is a smart solution for cleaning and surface finishing, which sets new standards for the post-processing of parts from powder bed fusion (PBF) AM technologies. The S1 can undertake cleaning and surface finishing all in one self-contained unit with the same media saving time and costs. This 2-in-1 concept (running two post processing steps in one single machine), combined with a higher degree of automation, streamlines the entire AM process chain and substantially reduces cost per piece.
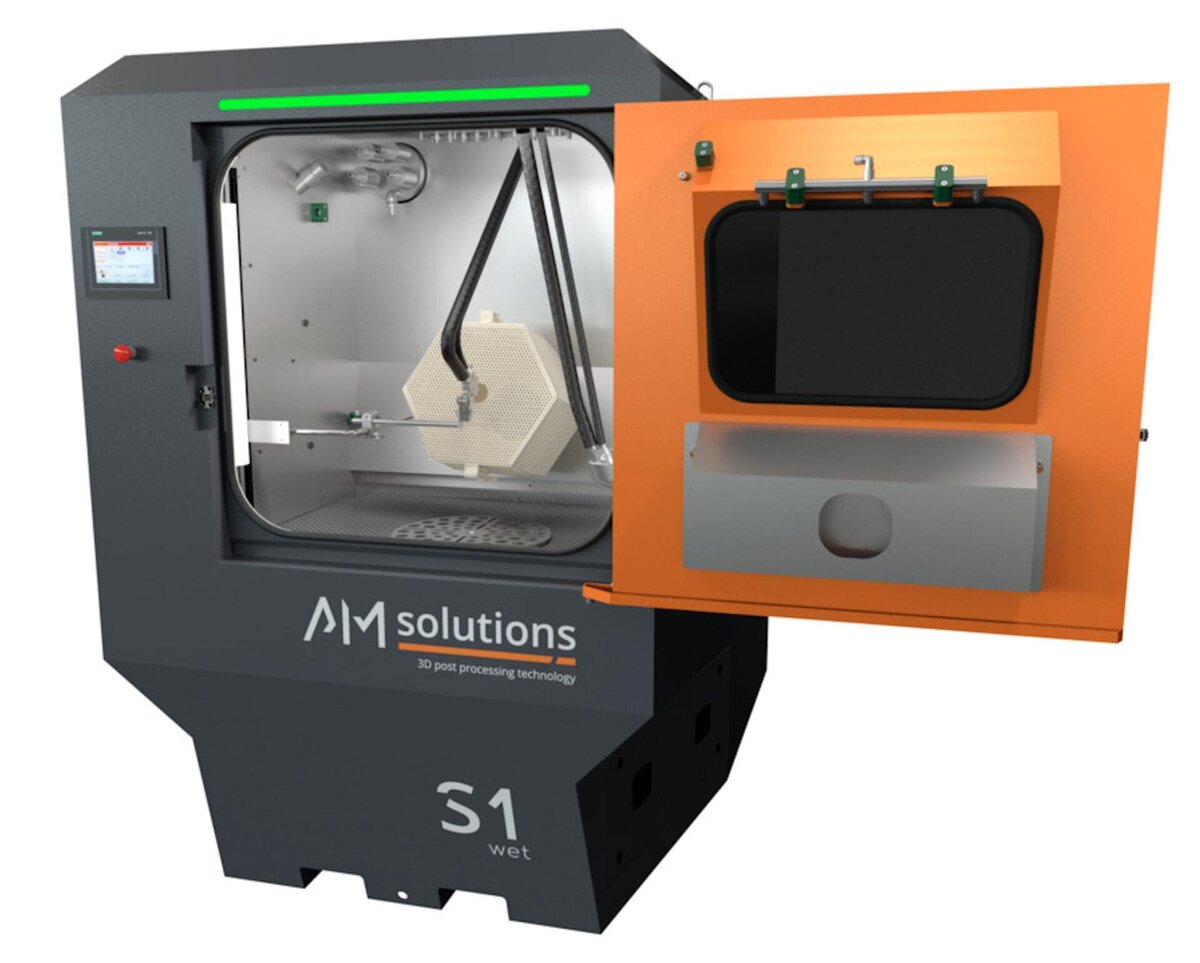
The S1 Wet, a versatile wet-blasting solution for cleaning and finishing surfaces on metal and plastic parts.
Such an approach allows the us to perfectly fulfil the requirements of customers who are looking for high volume production with 3D printing technologies.”
Also on show at Rapid-TCT will be the M1 Basic all-round post processing solution for the surface smoothing and polishing of single parts and small batches; the C1 system which is a machine for the automated and cost-efficient post-processing of photopolymer components; and the S1 Wet, which can process metal or plastic parts individually or in batches.
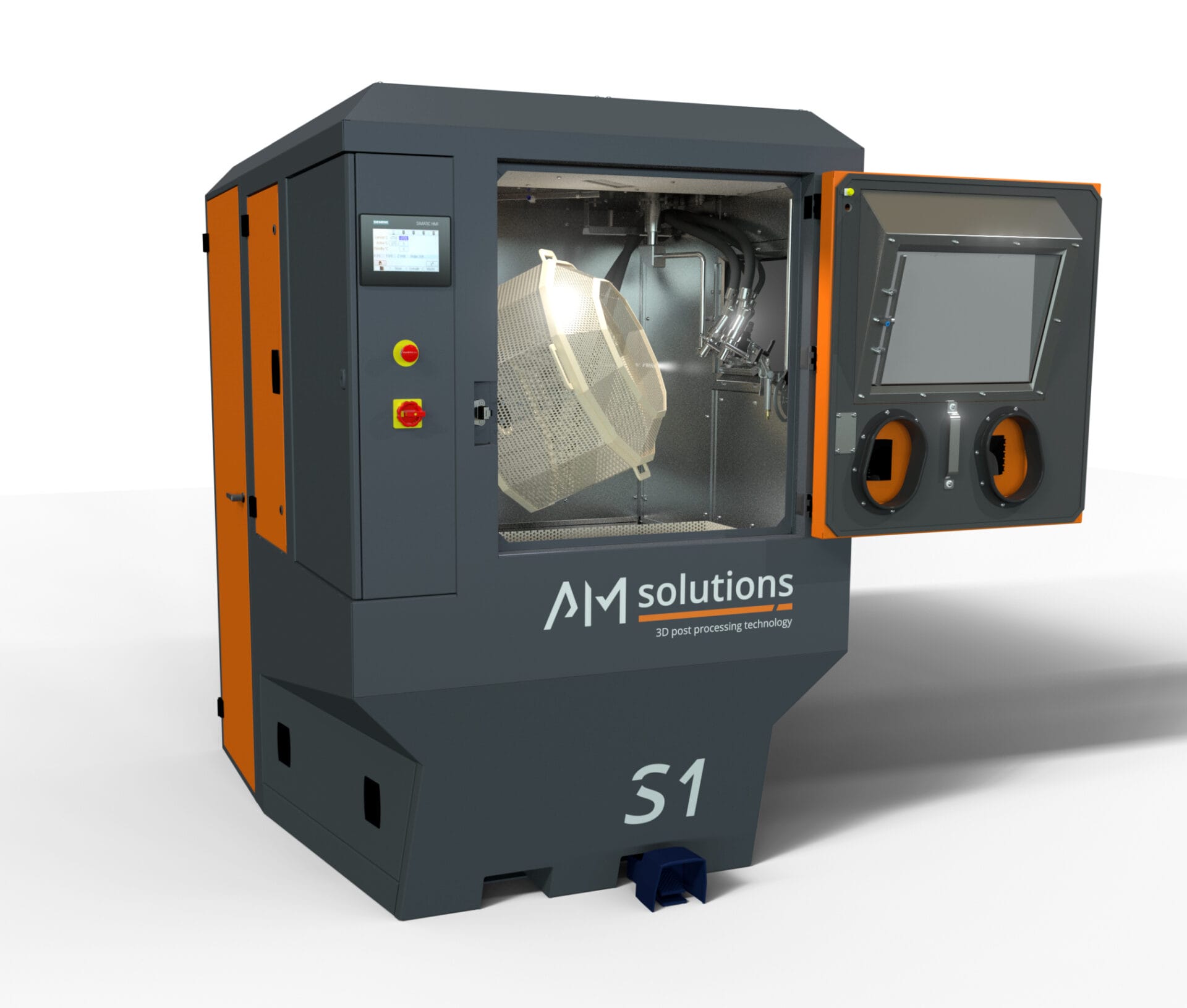
The S1 — a smart solution for cleaning and surface finishing, which set new standards for the post-processing of parts from powder bed fusion (PBF) AM technologies.
Sigirtmac concludes, “One enormous benefit of the S1 Wet on show at Rapid-TCT is the fact that wet blasting is not affected by ATEX regulations as there are no dust explosion risks, a major headache when using dry blasting on materials especially titanium or aluminium. The risk of dust explosion is considerably higher for AM produced parts than for conventionally machined parts as there is always some residual printing powder left on the parts, so this is a game-changer AM post-processing solution. Come and see the S1 and all our other machines on booth 1229 at Rapid-TCT, and let us show you the future of AM post-processing today.”