~ Omniflex and Deakin University’s collaboration wins Corrosion Innovation of the Year Award ~
Researchers at Deakin University have won the Corrosion Innovation of the Year Award at this year’s AMPP Annual Conference and Expo in Nashville, USA. The award recognised the development of a novel closed-loop cathodic protection (CP) system for localised corrosion control in challenging industrial environments, which Omniflex helped with as a technology partner. The probe is ideal for use in applications including floating wind turbines and underground or subsea oil and gas pipelines.
Since 2014, the Corrosion Innovation of the Year Awards have provided a forum for showcasing the latest innovations in corrosion control with winners selected by a panel of industry experts. This year, the awards received a record-breaking 60 nominations covering areas like coatings and linings, equipment, testing, monitoring, chemical treatment and more.
The closed-loop probe is the outcome of several years of research by the team at Deakin University, supported by Omniflex and other specialist partners, and it has been shown to facilitate better-than-ever localised corrosion control in complex and varying environmental conditions. The potential applications include protecting offshore structures, such as wind turbines and oil and gas platforms, and underground infrastructure, like steel pipelines and storage tanks.
“Prototype field tests for the CP probe demonstrated the technology’s ability to reduce corrosion by approximately 90 per cent and this could help to more than double operational lifetimes, making installations more sustainable and cost effective,” explained David Celine, managing director of Omniflex. “With prototype field tests now completed, the project is entering the commercialisation phase and is now available to the wider CP market.”
Professor Mike Tan, professor of applied electrochemistry and corrosion techniques at Deakin University, added, “Currently, corrosion under disbonded coatings is a major issue impacting the safe operational life of underground gas pipelines and future hydrogen pipelines. Another key problem that the technology addresses is the lifecycle of offshore wind farms, which is currently too short at around 25 years. This is unsustainable from a lifecycle assessment perspective.”
Omniflex worked with the Deakin University team to develop the technology’s electronics, integrate sensors and facilitate remote monitoring and control capabilities.
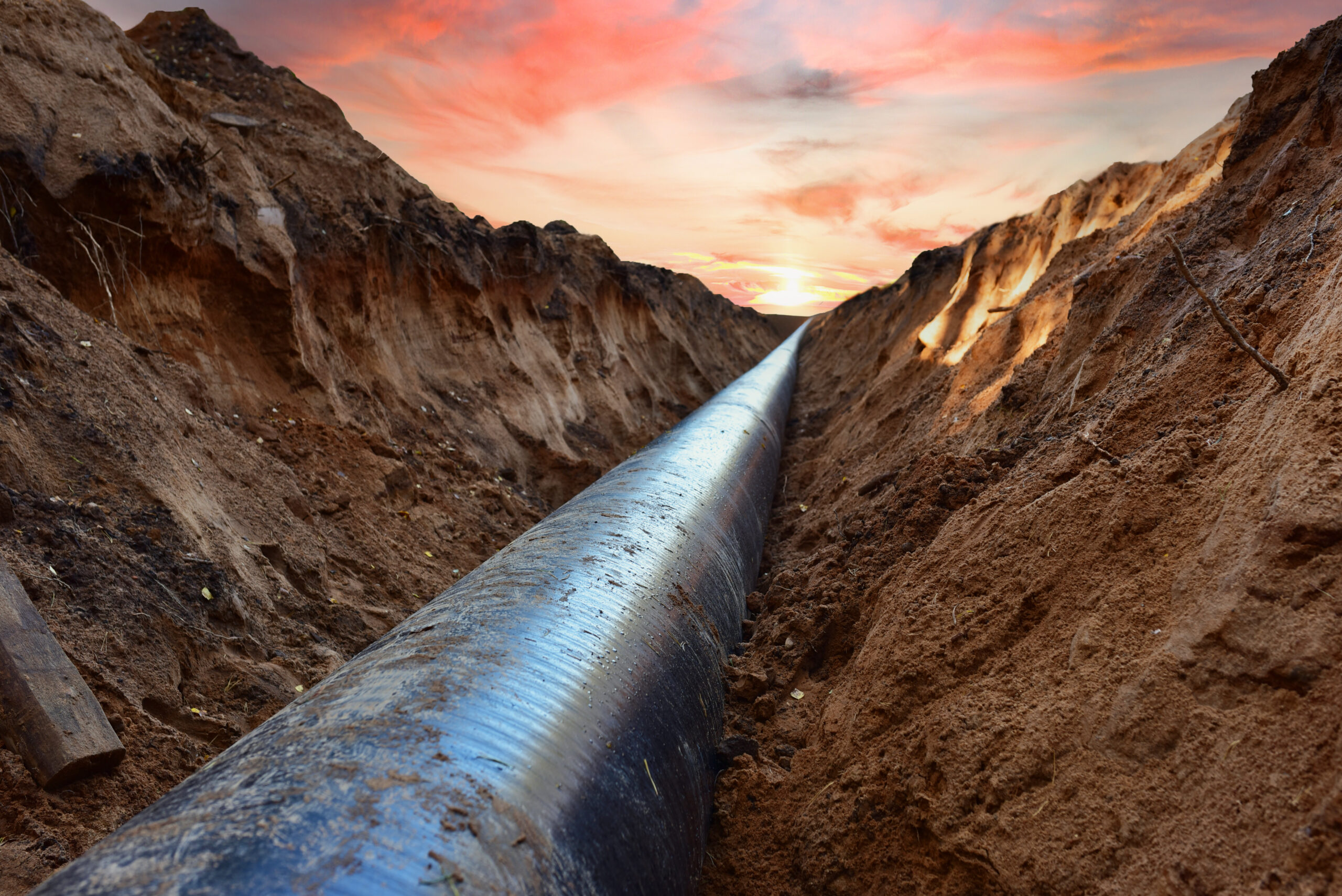
“Traditional CP systems don’t adjust output voltages and currents to compensate for constantly varying environmental conditions, meaning there is a risk of over- or under-protection,” continued Celine. “Beyond simply wasting energy, overprotection can harm structures by producing hydrogen and causing embrittlement, ultimately causing structural failure. Thanks to its built-in remote monitoring and control capabilities, the closed-loop CP probe can adjust protection levels for ongoing variances to consistently maintain optimal protection levels.”
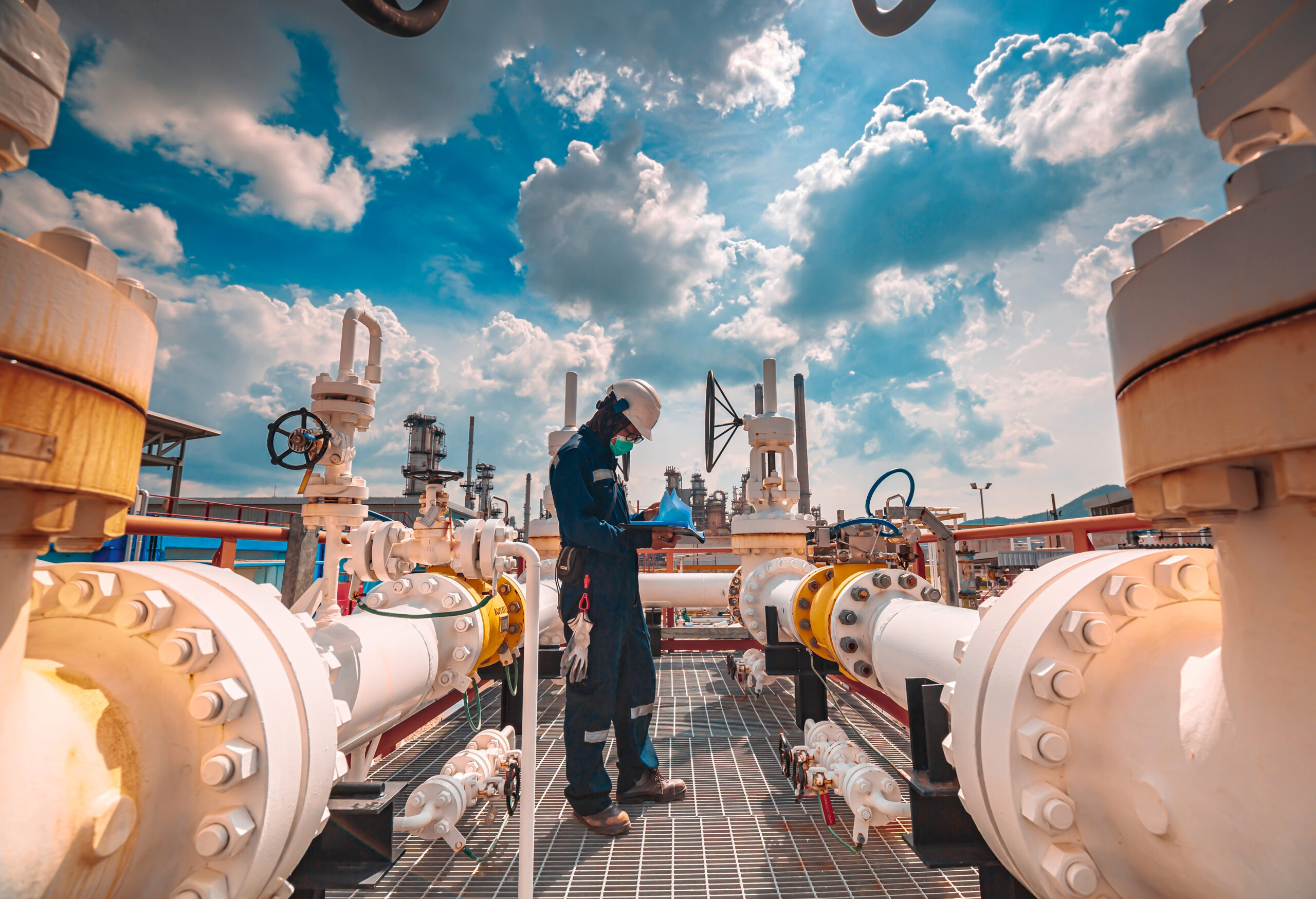
Professor Tan concluded, “We chose Omniflex as the equipment manufacturer and supplier as it is the only company who can provide the unique set of skills that we are looking for as a partner. We have worked with them since 2017 and will continue to work together on various projects for the global CP market in the coming years.”
The closed-loop CP probe has now completed field testing on underground pipelines and is entering the commercialisation phase of the project, backed by the Australia Economic Accelerator fund. To find out more about the probe and how it can help you overcome localised corrosion challenges, contact Omniflex.