Horizon Microtechnologies is making significant strides in validating the robustness of its proprietary metal coatings for micro additive manufacturing (AM) and 3D micro fabricated parts. At the beginning of an extensive testing initiative, the company has subjected its copper coatings (passivated using a new method) to a series of pragmatic tests meant to emulate a number of environmental stresses that industry is usually concerned about. The results of these tests demonstrate a high level of resilience, reinforcing the viability of Horizon’s technology for demanding applications, including electronics, RF components, and even space systems.
Passivation is a crucial process for preventing the natural ageing of metals such as copper. Without protection, exposure to humidity, oxygen, and extreme temperatures can degrade copper coatings and surfaces, leading to oxidation, loss of conductivity, and in some cases, compromised adhesion to underlying structures. These concerns are particularly relevant in advanced applications where the electrical and structural integrity of metal coatings must be maintained over long periods. While various methods exist to improve copper’s durability — such as the application of metallic overcoats, alloying, or using additional protective films or surface treatments — these conventional solutions are often optimised for specific part geometries or material systems, such as printed circuit boards, and are not necessarily effective or easy to implement for the intricate 3D-printed products that Horizon specialises in.
To address this bottleneck, Horizon Microtechnologies has developed its own passivation process, engineered specifically to protect copper coatings on complex 3D-printed microstructures. Recognising the industry’s concerns regarding the applicability of such coatings in non-controlled environments, the company initiated a series of internal stress tests designed to replicate some of the harshest environmental conditions a coated component might experience. The goal was to determine whether its passivated copper coatings could withstand high temperatures, extreme humidity, and exposure to chemically aggressive conditions, such as atomic oxygen — something that is particularly relevant in space applications.
Heat Benchmark
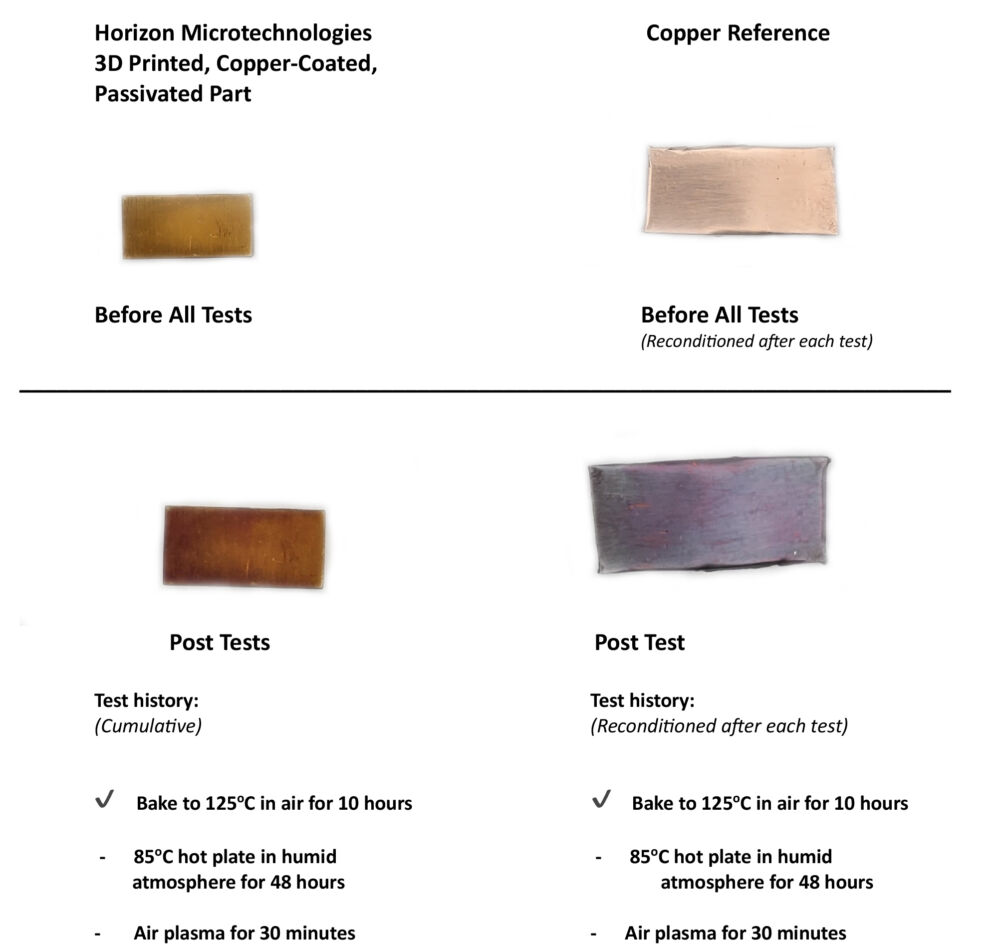
Humidity Benchmark
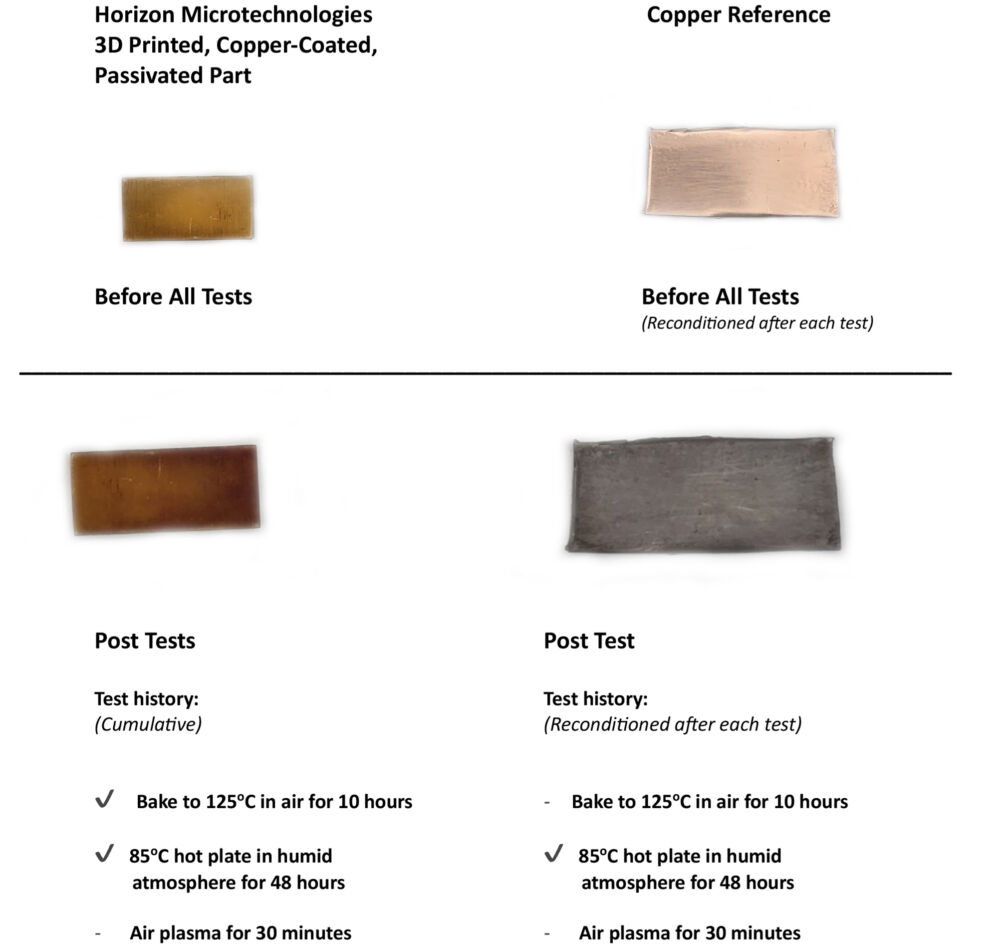
Plasma Benchmark
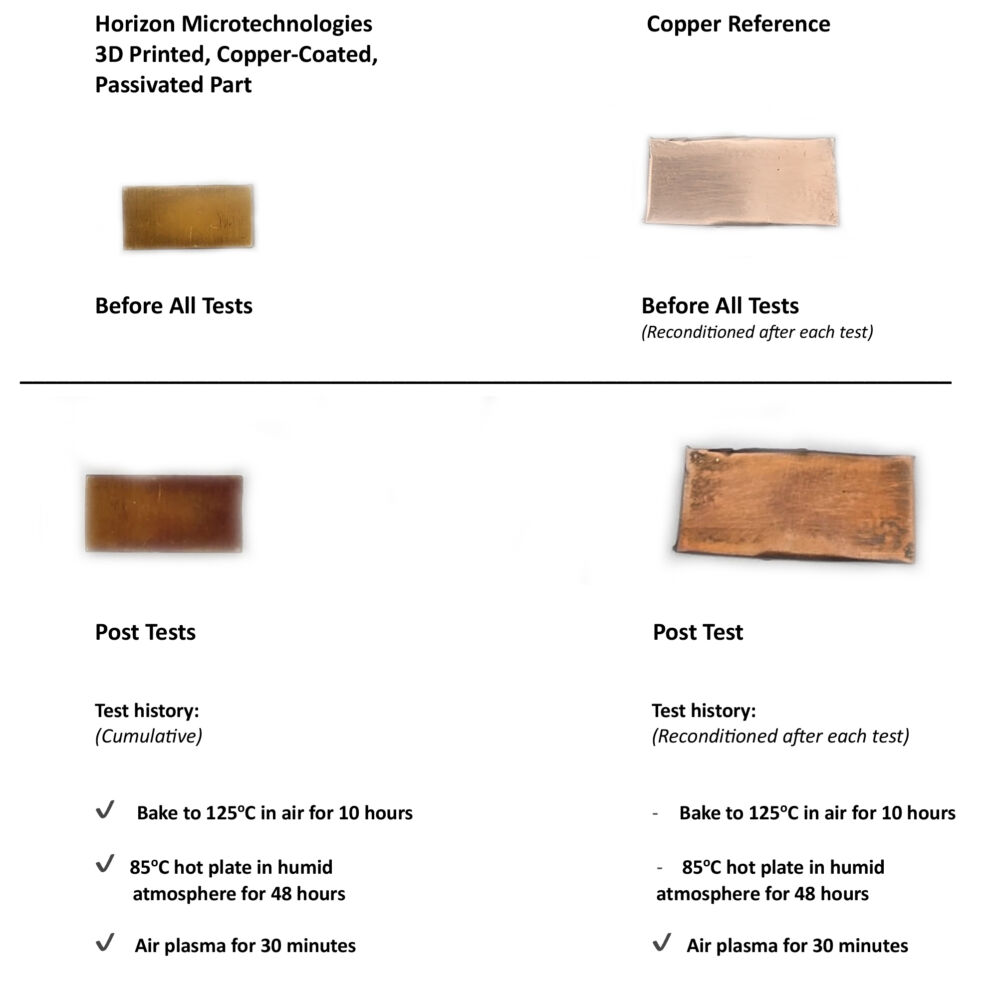
The results of these tests clearly demonstrated the superior stability of Horizon’s passivated copper coating. Across all tests conducted — including high-temperature exposure, prolonged hot humidity, and air plasma exposure — the passivated copper coating remained visually and electrically unaffected except for a small colour change during the initial heating, while standard reference copper suffered significant degradation under the same conditions. Cold exposure tests were also conducted, where both materials showed no visible changes. These findings highlight the remarkable resilience of Horizon’s coating, reinforcing its potential for demanding industrial and aerospace applications where material stability is critical.
The results indicate that Horizon’s passivation process is highly effective in protecting copper coatings against common ageing mechanisms, positioning the company’s technology as a robust solution for high-performance applications. With additional long-term testing according to industry standard test conditions forthcoming, these early findings offer strong evidence that Horizon’s passivation method provides substantial protection, ensuring the longevity and reliability of its coated micro-AM parts.
“Taken by themselves, our tests demonstrate that concerns about copper ageing on 3D-printed or 3D micro fabricated parts are largely unfounded for a large set of use cases when our passivation technology is applied and they are an extremely encouraging result with a view to long term stability,” says Andreas Frölich, CEO at Horizon. “By proactively addressing oxidation and degradation challenges, we are demonstrating that our coatings are well-suited for applications requiring high durability and environmental resistance.”
With these promising results in hand, Horizon Microtechnologies continues to refine its processes and expand its validation efforts. The company remains committed to delivering cutting-edge microfabrication solutions that meet the highest industry standards for performance and reliability.