The world’s railway network spans over 1.3 million route-kilometres. Urban and high-speed rail infrastructures have scaled up rapidly over the past decade, laying the foundation for convenient, low-emissions transport. As one of the most efficient modes of transport for freight and passengers, continued investment in rail forms a high priority for a more sustainable, resilient future. But how can this look from an engineering level? Here Harish Maniyoor, Manager – Offer Implementation Turning, at metal cutting and manufacturing solutions expert Sandvik Coromant, explores.
According to the International Energy Agency, rail is among the most energy efficient modes of transport — representing just 2% of total transport energy demand, while accounting for 8% of world passenger and 7% of global freight transport. It’s easy to see why, then, world leaders are taking rail investment seriously.
Railway advancements
In Europe, significant investments are being made to double high-speed rail traffic and increase rail freight volumes by 50% by 2030, as part of the European Union’s sustainable mobility strategy. Elsewhere, the Biden Admistration announced nearly $30 billion in investments for rail projects, demonstrating a commitment to enhancing rail infrastructure and service.
Perhaps most significant of all, the railway sector in India has undergone many developments in recent years, driven by government initiatives like dedicated freight corridors (DFCs), high-speed rail projects and the modernisation of railway infrastructure.
But, to continue driving progress, rail infrastructure will need to undergo substantial upgrades and expansions to meet rising demand, ensure safety and accommodate technological advancements. This includes modernising aging rail networks, increasing capacity through electrification, implementing advanced signaling systems and integrating digital technologies for more efficient operations.
Meeting tough demands
The production of railway components such as axles, wheels, railway tracks, suspension tubes and other structural parts requires high-quality machining tools, capable of delivering exceptional accuracy, durability and efficiency. These components must withstand heavy loads, intense wear and harsh environmental conditions, making precision machining critical to ensuring the reliability and safety of rail systems. High-quality machining tools must offer tight tolerances, consistent performance and the ability to work with a wide range of materials.
Take rail wheels, for instance, which are subject to extreme stresses and wear from continuous contact with rails, often under heavy loads and at high speeds. Several machining challenges present themselves here. First is the need to maintain very tight tolerances, with even a slight deviation from the specified dimensions possibly leading to issues like uneven wear, vibrations or noise during train operation, compromising both passenger comfort and safety.
Another major challenge is working with materials that can withstand the intense mechanical stresses and harsh environmental conditions trains are exposed to. Train wheels are typically made from high-strength steel or steel alloys with excellent fatigue resistance and wear properties. However, these materials are often difficult to machine due to their hardness and toughness. As a result, thermal management during machining is also a key consideration. Machining high-strength steel generates significant heat, which can cause thermal deformation in the workpiece, affecting dimensional accuracy.
It’s important to recognise that components for different rail types will present their own sets of requirements. Freight trains for instance are heavy, hence the wear on the wheels is high and brake marks from cargo cars often appear on the outer diameter of the wheels. Metro wheels, in contrast, are far smaller and may feature rubber layers between the outer diameter of the wheel and hub to minimise noise. On the other hand, those operating on high speed rail networks have high demands on exact wheel dimensions, as it is directly related to the comfort of the passenger. To ensure that the wheels are balanced, the tolerances on the outer diameters are high and wheels are frequently re-tuned.
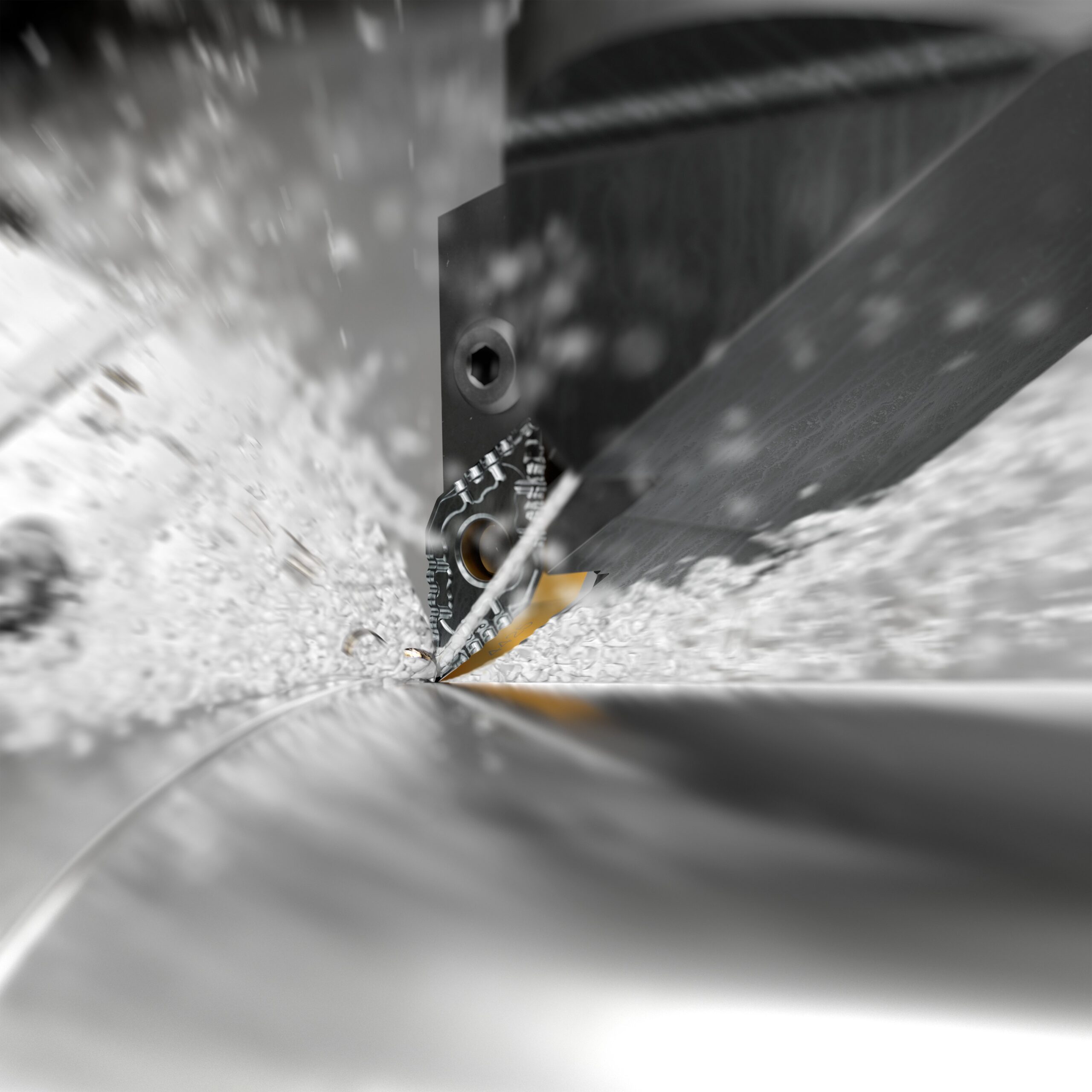
Action Image of T-Max P with HP and insert grade 4425
On track with precision machining
There are several machining strategies that, when paired with robust machine tools, can support the production of resilient rail components. Heavy turning is an excellent strategy for machining rail components due to its ability to handle the large components and high-strength materials, as well as its efficiency and precision when working with complex shapes and heavy-duty parts.
When performing heavy turning for rail components, tool life can be significantly improved by focusing on a few key factors. First, choose a cutting tool with a strong, wear-resistant grade that suits the material’s hardness, ensures stability throughout the cut. Minimise cutting forces by using the right feed rate and depth of cut to balance tool pressure, and always ensure proper coolant application to control heat and prevent thermal deformation. Finally, ensure the tool setup and machine stability are optimised to handle high forces and maintain accuracy in turning.
Sandvik Coromant recommends the T-Max® P product range for external turning, offering enhanced cutting stability, improved chip control and extended tool life to enable precise and efficient machining of tough rail components such as wheels and axles. Optimised for external turning, from roughing to finishing, T-max® P handles medium to large components in steel, stainless steel, cast iron, heat-resistant alloys and hardened steel. Available with high precision over and under coolant and Coromant Capto® quick tool change interface, high stability and minimised tool inventory can be easily achieved in rail machining.
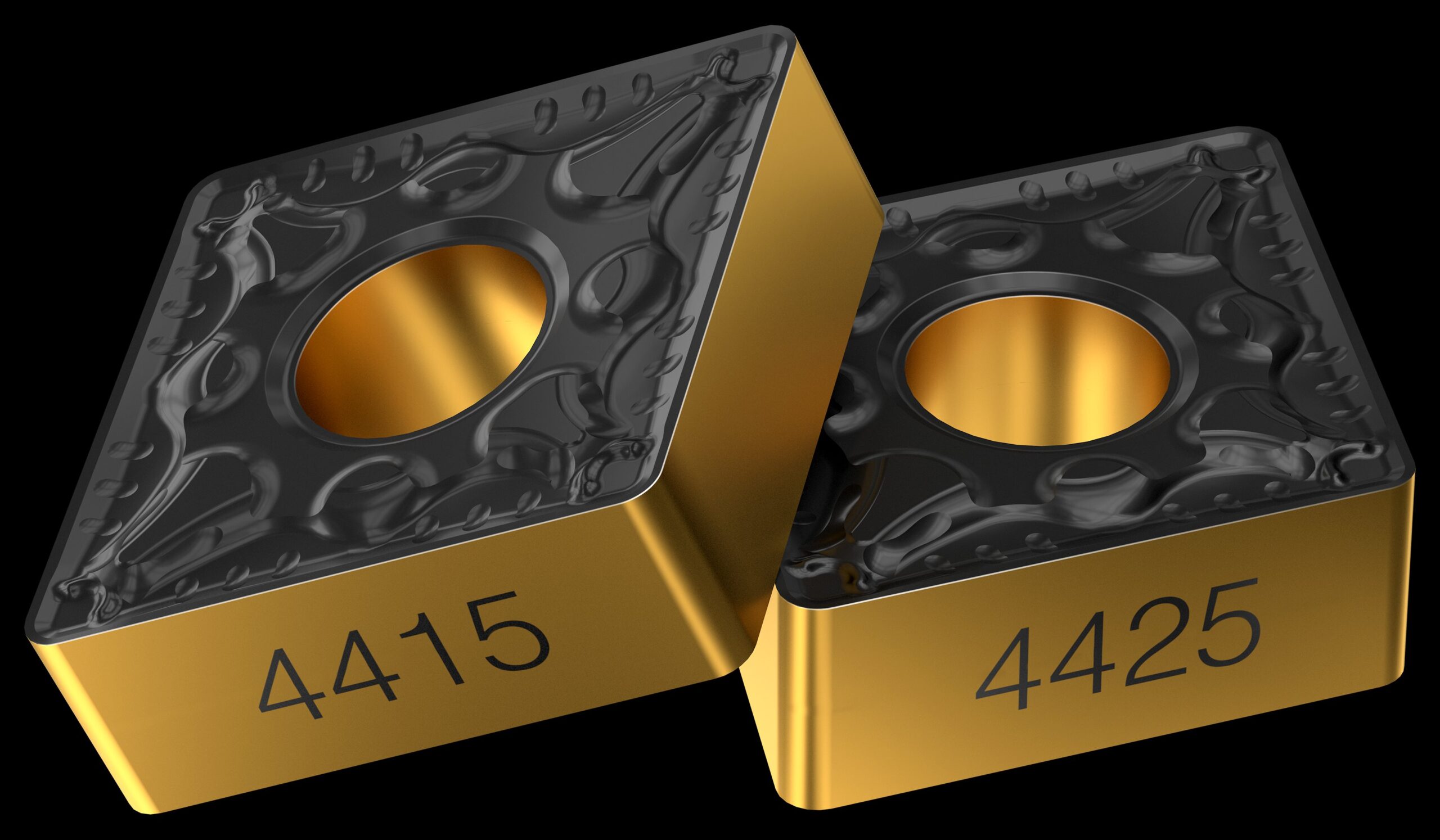
GC4425 GC4415 T-Max P insert collection
Additionally, Sandvik Coromant offers expert recommendations on the most suitable turning grades for your rail application, ensuring a complete machining solution tailored to the specific requirements of the workpiece.
The future of rail infrastructure hinges on precision machining and innovative technologies to meet increasing demands for safety and efficiency. By focusing on effective machining strategies and tailored recommendations, we can ensure that the rail industry not only meets today’s challenges but also paves the way for a sustainable and efficient transportation network for the future.