Methyl methacrylate structural adhesives (MMAs) offer strength, toughness, and ease of use when bonding metals, plastics, and composites. Their properties and processing benefits mean they are suitable to trial for many applications including in the marine, transportation, and sign-making industries. Compared with alternative chemistries like epoxies and polyurethanes (PUs), the benefits and properties of MMAs are perhaps less well known. Here Ben Swanson, Joint Managing Director at adhesives specialist Intertronics, shares an overview of this useful adhesive technology.
A structural adhesive is one that cures into a material capable of holding two or more substrates together, bearing the forces involved for the lifetime of the project, such as shock, vibration, chemical exposure, temperature fluctuations, or other destructive/weakening agents. Common structural adhesives are epoxies, PUs, UV curing adhesives, MMAs, and arguably cyanoacrylate adhesives.
What are MMAs?
MMAs are two-part reactive acrylic adhesives that include a resin and an activator. Mixing them together causes a free-radical reaction that enables fast curing at room temperature. Additives may include elastomeric tougheners and impact modifiers. They are typically available in two mix ratios, 1:1 and 10:1. The 1:1 adhesives generally have higher strength than the 10:1 products, but the 10:1 adhesives have higher elongation, and so more flexibility.
MMAs are excellent for bonding metals (steel, stainless steel, aluminium), thermoset composites (both carbon fibre and glass fibre reinforced), and thermoplastics (acrylics, ABS, polycarbonates, PVC, and other engineered plastics). They are favourable in applications where fast cure speed, strength, toughness, and environmental resistance are important. Because they bond to a wide range of substrates, and have choices of cure speed, they are seen as quite versatile. Certain formulations have approvals from Lloyds and the American Bureau of Shipping, and meet FST for interior rail applications, as well as having approvals from automotive manufacturers.
Process benefits of MMAs
MMAs fully cure and reach their full strength at room temperature, due to the fast exothermic reaction that forms them. Their cure is less susceptible to ambient conditions like temperature and humidity than other adhesives. Critically, the time between mix/application and fixture strength (enough cured strength to allow further processing, sometimes called green strength or handling strength) is short, reducing work in progress and enabling faster throughput — a key processing advantage. To suit different process requirements, MMAs are available with a range of working times (5 minutes up to 120 minutes) and fixture times (6 minutes up to 4 hours).
Typically, less surface preparation is required when using MMAs to bond composites, metals, and plastics than when using other adhesives, as the chemistry is able to cut through some surface contamination. A solvent wipe to remove any light oils on metals or composites, or a dry wipe on plastics, may be all that is required with an MMA, although some projects will require the use of a solvent wipe or abrasion. Some MMA products are available that bond metal without the need for a primer, which creates a leaner process, removes the risk of error, and can improve health and safety.
Methyl methacrylate adhesives are readily and commonly available in two-part cartridges from 50 ml to 490 ml in size, and can be supplied in bulk for larger volume applications. They are applied through static mixing nozzles, which comfortably give the adhesives an adequate mix.
Properties of MMAs
Important properties for a structural adhesive are strength, toughness, and flexibility. When bonding dissimilar materials, such as a rigid metal with a flexible plastic, flexibility in the adhesive is particularly important.
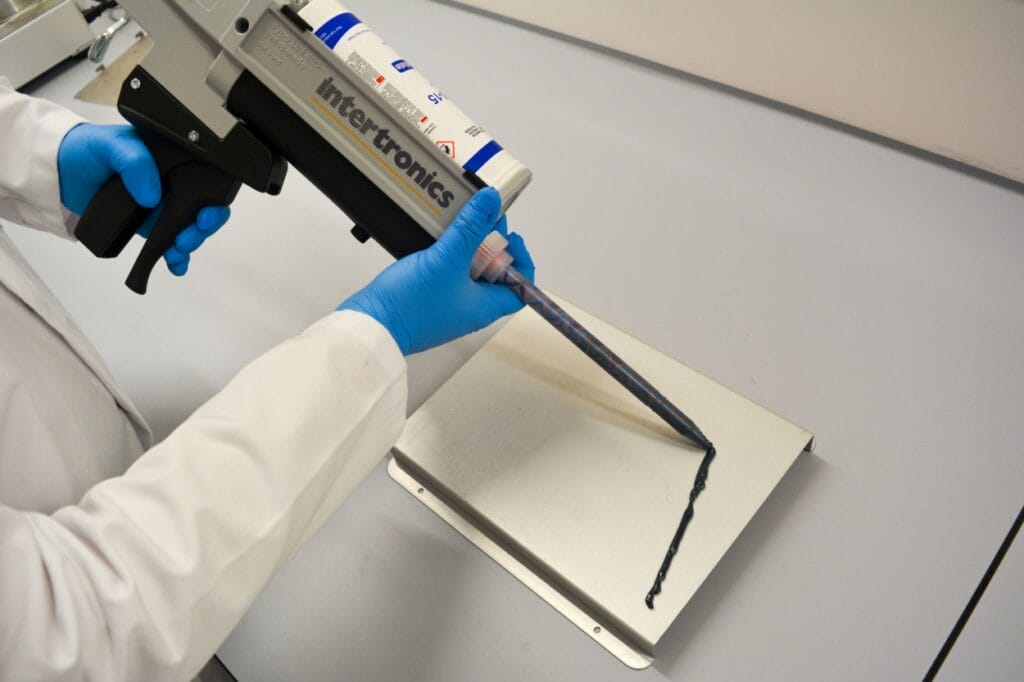
With a crosslink density between that of epoxy and polyurethane, SCIGRIP’s MMA technology combines high strength with good flexibility. Generally, when compared with epoxy technologies, MMAs are less brittle, less prone to cracking, offer non-critical mix ratios, large gap fills, and a flexible choice of cure speed. When compared with polyurethanes, MMAs offer high bond strength, good impact resistance, large gap fills, less environmental sensitivity, good chemical and environmental resistance, fast cure speed, and reduced health risks (no isocyanate).
In metal bonding, for example, MMAs have become a popular choice over epoxies, as they are easier to use and cure faster, whilst having enough bond strength for many applications.
Some disadvantages
Acrylic adhesive technology does have a stronger odour than other chemistries, although all SCIGRIP MMAs have GREENGUARD certification for low VOC and chemical emissions. MMAs have lower operating temperature ranges than, say, epoxy adhesives. In some cases, where there is larger adhesive mass or thicker bond lines, understanding of the exothermic heat produced during fast cure is required to avoid potential substrate discolouration or distortion.
Summary
It is important to note that there is no perfect or universal adhesive, and the benefits and disadvantages of each chemistry should be weighed up against the demands of the application and processing environment. Overall, MMAs bring many process and technical advantages to applications in a range of industries, and may be a good candidate to trial when reviewing structural adhesive chemistries.
To find out more about SCIGRIP MMA adhesives, contact Intertronics +44 (0) 1865 842842 to speak to a specialist. For more information on the product range, visit https://www.intertronics.co.uk/scigrip-structural-methyl-methacrylate-adhesives-mmas/.