In the fast-paced world of mass manufacturing, delays compromise productivity. Eradicating their causes – whether through malfunction or maintenance – is key to ensuring uptime, efficiency and customer satisfaction.
Automatic Guided Vehicles (AGVs) play an essential role in today’s modern manufacturing environment. Whether they are moving partially completed goods through different stages of production, transporting materials or components from storage to production lines or between workstations, their role underpins the efficient flow of goods throughout the manufacturing process. Given AGV’s role in the workflow, any downtime they experience can have serious consequences.
Carrybots takes the weight off conveyors
One AGV manufacturer that has been helping companies easily and cost-efficiently achieve transport automation, is Carrybots GmbH. Founded in 2021, its popular mobile robots for in-house logistics -– including HERBIE – stand out for their high levels of modularity, flexibility and the modern control software incorporated into its products. It is recognised that the consolidation of load carriers – especially when the return of empty containers is required – poses significant challenges for manufacturers of conveyor technology. This leads to high costs and inflexible space utilisation for customers. HERBIE addresses this challenge by automating this process without compromising the benefits of conventional conveyor technology.
Recently, Carrybots responded to a request from a large tea manufacturer that had a requirement for a HERBIE with a faster, more convenient method for charging. Carrybots weighed up the pros and cons of battery swapping versus automatic charging, and concluded that battery swapping takes more time, while in process charging could be realised through a wireless solution. The latter option brings many advantages in a production or in-house logistics environment, ranging from improved safety, faster charging times and easier implementation. It also negates the need for additional storage space to house batteries while they are charging.
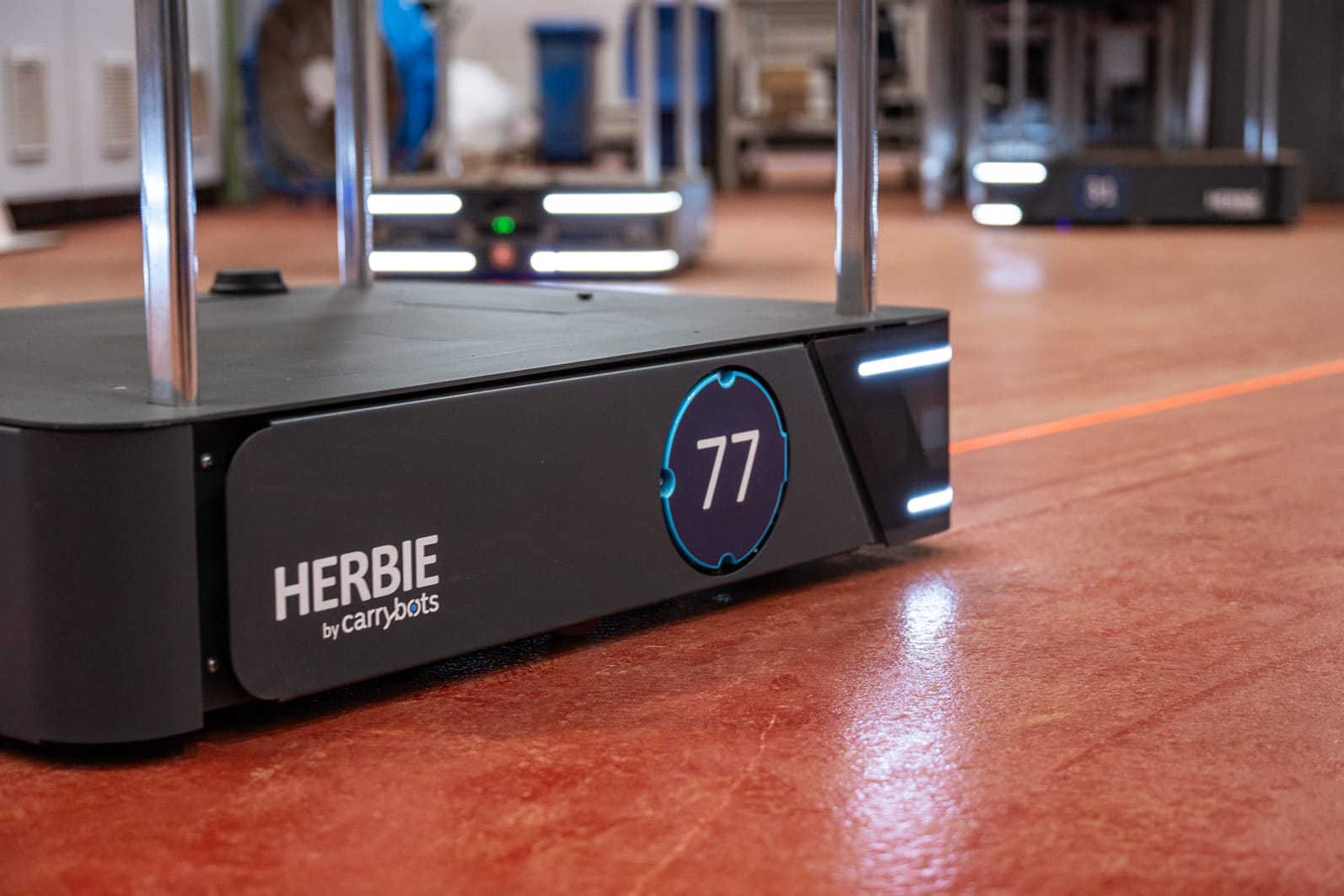
With the preferred charging method established, the tea manufacturer then identified certain requirements that the wireless charging solution had to fulfil. It had to offer minimal to no maintenance and be high quality. Due to the nature of the manufacturing environment, it also had to be suitable for harsh environments (especially dusty ones) and have no open contacts. It needed to offer CAN communication, be compact on the AGV while also being easy to integrate into the facilities. With those requirements established, Carrybots’ next step was to identify the manufacturer best able to meet the customers’ wireless charging needs.
Where Delta leads, others follow
With its rich heritage in power electronics and industrial battery charging, the breadth of its portfolio and its considerable experience in the manufacturing sector, Delta is recognised throughout the AGV, AMR and other industrial e-vehicle manufacturer as the go-to company for battery charging. Its wireless charging solutions are renowned for efficiency of up to 95% within a gap of up to 150 mm, IP 65 and the most reliable PPL communication*.
Given its reputation for innovation, naturally Delta was the first company to offer a 1kW Wireless battery charging system in series production. It now offers the broadest range of wireless charging systems that scale from 1 kW to 3.3 kW, 10 kW and 30 kW outputs. Delta is also recognised for its levels of customer and technical support, and its willingness to offer testing material to make it easier for customers to establish the most suitable solution for their requirements during the Proof-of-Concept stage.
Those qualities appealed to Carrybots, embodied as they are into Delta’s MOOVair wireless charging systems, a revolutionary, no maintenance, high-efficiency product ideal for charging batteries in AGV/AMRs and all kinds of industrial electric vehicles. Furthermore, MOOVair guarantees reliability in dusty environments. The other charging alternatives that Carrybot considered used IR-communication – which, when covered by dust, could cause communication issues – and were ruled out on safety and reliability grounds.
Uptime at all times
Commenting on its decision to opt for MOOVair, Marcel Meckes, Carrybots Managing Director, stated: “Wireless charging systems are easy to integrate within the facility without altering the space. The MOOVair System appealed to us for being compact in size and the 1 kW system is flexible enough to be ‘docked’ even to the existing residential power plugs. Thanks to MOOVair, automation of the process is even easier with automated charging; HERBIE stops by the charging system and charging starts automatically. This is as efficient as with contact charging solutions, but without wear or pollution that can cause charging issues..”
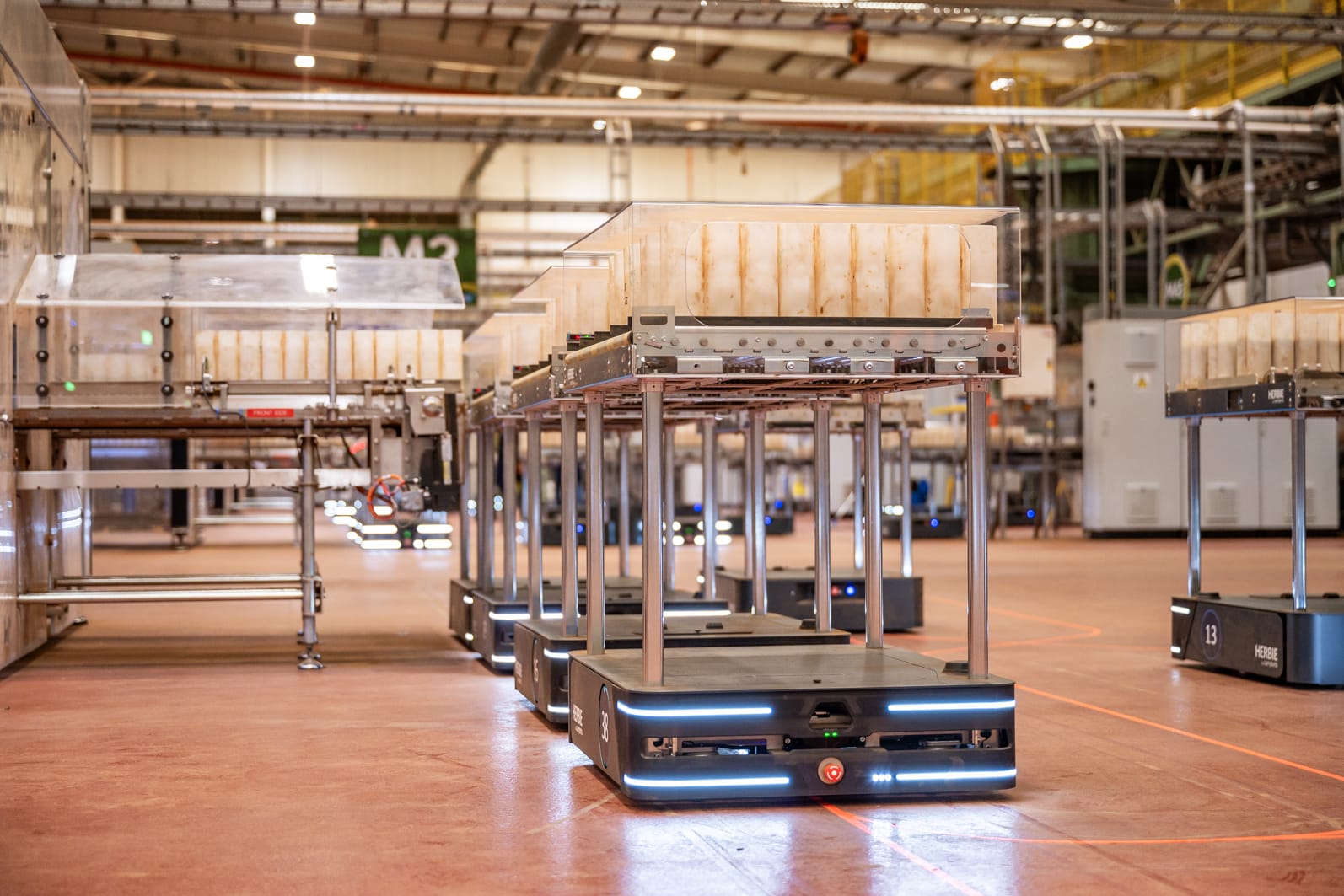
Sven Mayer, Sales Director IMBU added: “Efficiency and reliability lie at the heart of the modern manufacturing environment. Every part has a role to play in a complex eco-system that relies on uptime. In contrast to charging alternatives, Delta’s MOOVair wireless charging system is well suited such applications because, among other benefits, it avoids maintenance downtime due to torn or worn connectors. It also has IP65, and therefore it is suitable for harsh environments, including dust, dirt and moisture. It delivers on its promise of peak productivity, adding even more value to Carrybots’ solution.”
With the tea manufacturer now enjoying the performance and reliability of HERBIE – supported by the durable and rugged MOOVair wireless charging system – it can relax in the knowledge that charging has been simplified, downtime kept to a minimum and the production line flowing without interruption.