With its S1 shot blast machine from AM Solutions IFC company achieves top results within 70 % shorter cycle times
Individually designed orthopedic arm braces are one of many 3D printed products made by the IFC Intelligent Feeding Components GmbH. To guarantee a high degree of comfort for the patients, the braces must have an excellent surface finish. This is achieved with a recently purchased S1 shot blast machine from AM Solutions – 3D post processing technology.
The IFC Intelligent Feeding Components GmbH, located in the state of Baden-Württemberg, Germany, has not only expertise in innovative work piece feeding and assembly technologies, but the company has also a 3D print department equipped with state-of-the-art equipment. There, high-value 3D metal and plastic print products are made for a broad range of different industries. Frequently, IFC utilizes innovative scans to create specific component designs for the customers. Among other products, the company produces arm braces, which are individually designed and adapted by in-house orthopedic engineers.
To ensure a consistently high surface quality in the long run, the company decided to invest in a reliable and cost-efficient mechanical post processing solution. Dominik Riegg, managing the additive manufacturing department at IFC Intelligent Feeding Components GmbH, comments: „We tested many different systems, before we finally got to talk to AM Solutions at the Formnext 2022 exhibition. What impressed us immediately was that the equipment, built in-house, is very sturdy and, thus, can handle any industrial environment, no matter how demanding this might be. Moreover, the specialists at AM Solutions quickly understood what we need and with the S1 shot blast system they presented an optimal solution.“
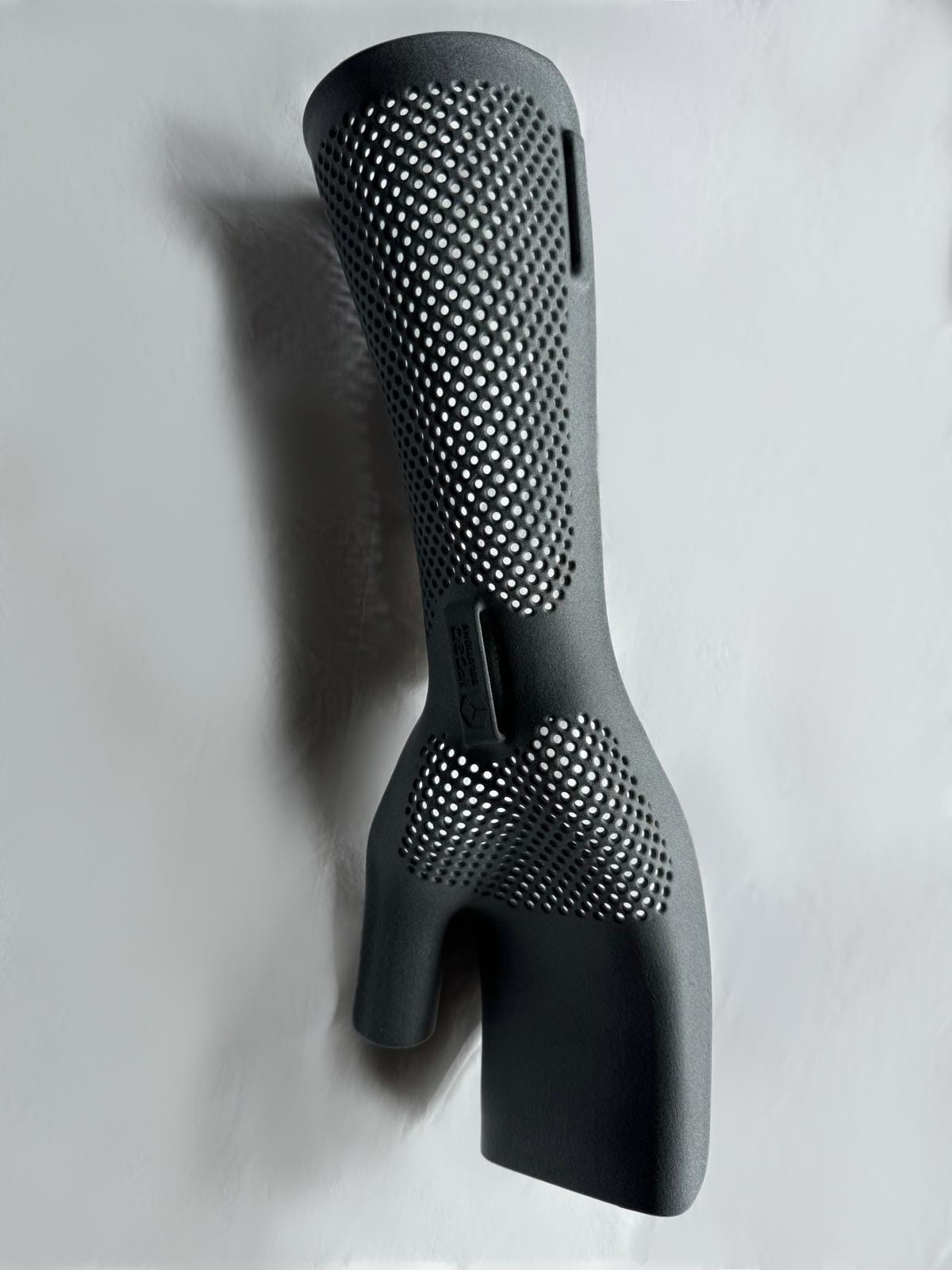
Arm Splint
Intelligent Feeding Components GmbH (IFC) uses 3D printing to produce, among other things, arm support splints that must be extremely comfortable to wear and require a reproducible surface finish
Poly beads vs. glass beads
At the AM Solutions Customer Experience Center in Untermerzbach, covering an area of 400 m2, the IFC engineers were able to thoroughly test the proposed equipment beforehand. At the same time, they could inform themselves about the most suitable blast media. Riegg continues: „We decided to use poly beads for our shot blasting process. This media may be a bit more expensive but offers a considerably longer service life than glass beads.” An additional advantage of the poly beads is that they create a surface finish that has a more pleasing color and a satin feel. „The glass beads penetrated the work piece surface, which can be highly problematic in the medical field. With the poly beads we achieve a smooth and highly homogeneous surface finish. This makes the wearing of the arm brace very comfortable,” explains Mr. Riegg.
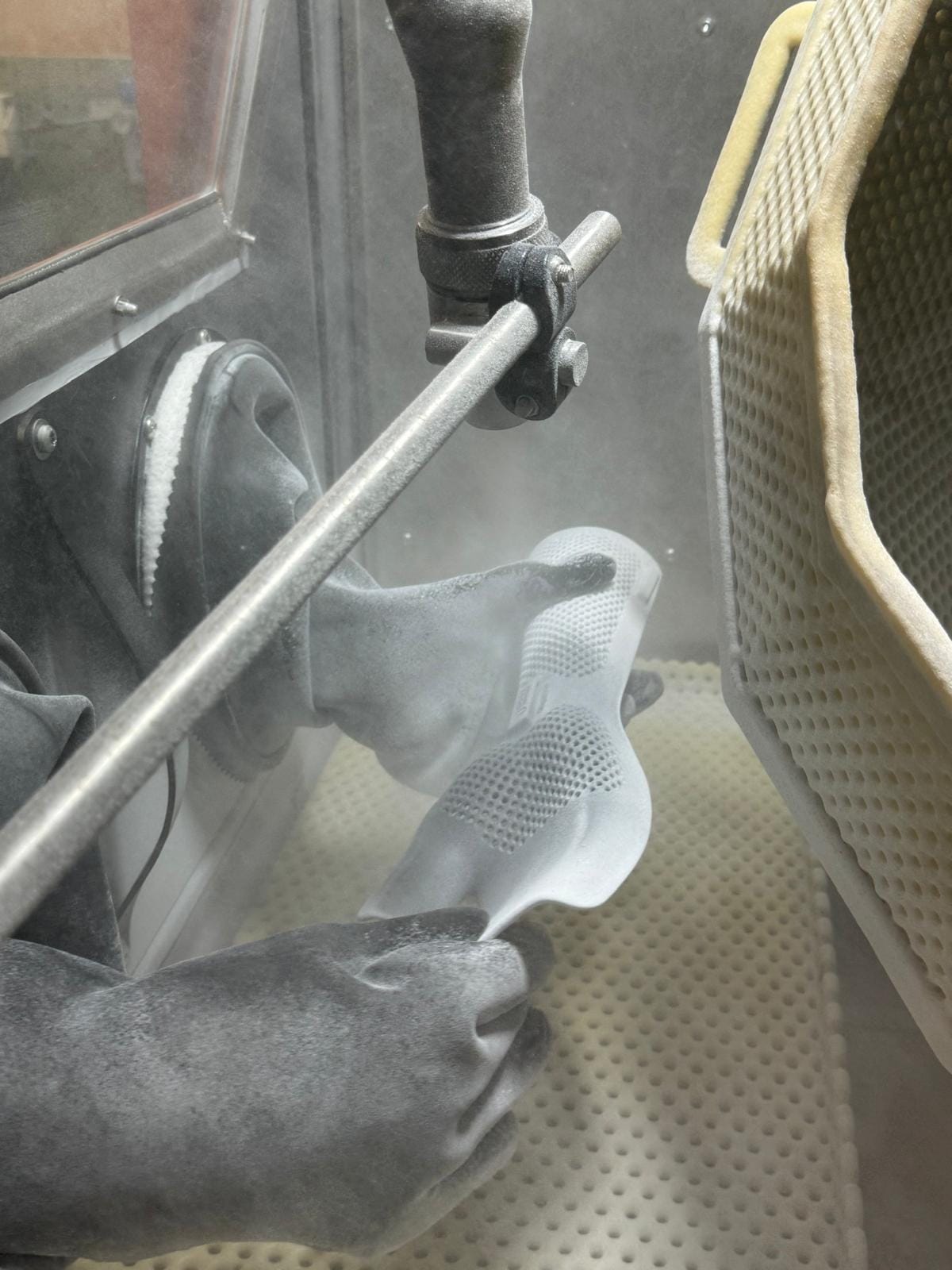
Blasting Processing
In the S1, the workpieces are cleaned and finished in a single step without changing the blast media. Polybeads are used as blasting media, which produce a smooth and absolutely homogeneous surface
Time savings of 70 %!
Prior to purchasing the S1 post processing system, the 3D print products had to be unpacked and shot blasted manually. Today, after the unpacking process they are directly loaded into the shot blast machine for cleaning and surface finishing in one single operation. This 2-in-1 solution requires only one single blast medium. The continuous rotation of the work pieces in the shot blast machine guarantees gentle processing and absolutely repeatable blast results. „With our manual shot blasting operation the finishing qualities were very unstable. Now we achieve consistent, high-quality surface finishes and, at the same time, save up to 70 % in labor costs “, explains Riegg.
Compared to the manual post processing operations, the S1 system handles a two times larger quantity of arm braces. And while the machine is running, the personnel is free to do other work. Riegg concludes: „Today we increasingly handle smaller work piece batches. To remain cost-efficient, we must automate our manufacturing operations and must have total process stability. Post processing is an essential link in our manufacturing chain and is a lot more than just making a product “pretty.” In the end, automated post processing is essential for achieving consistent, high qualities and allows us to expand our technological possibilities. Our S1 system amortized itself in 1.5 years, but its positive effects for our production will last for a long time.“
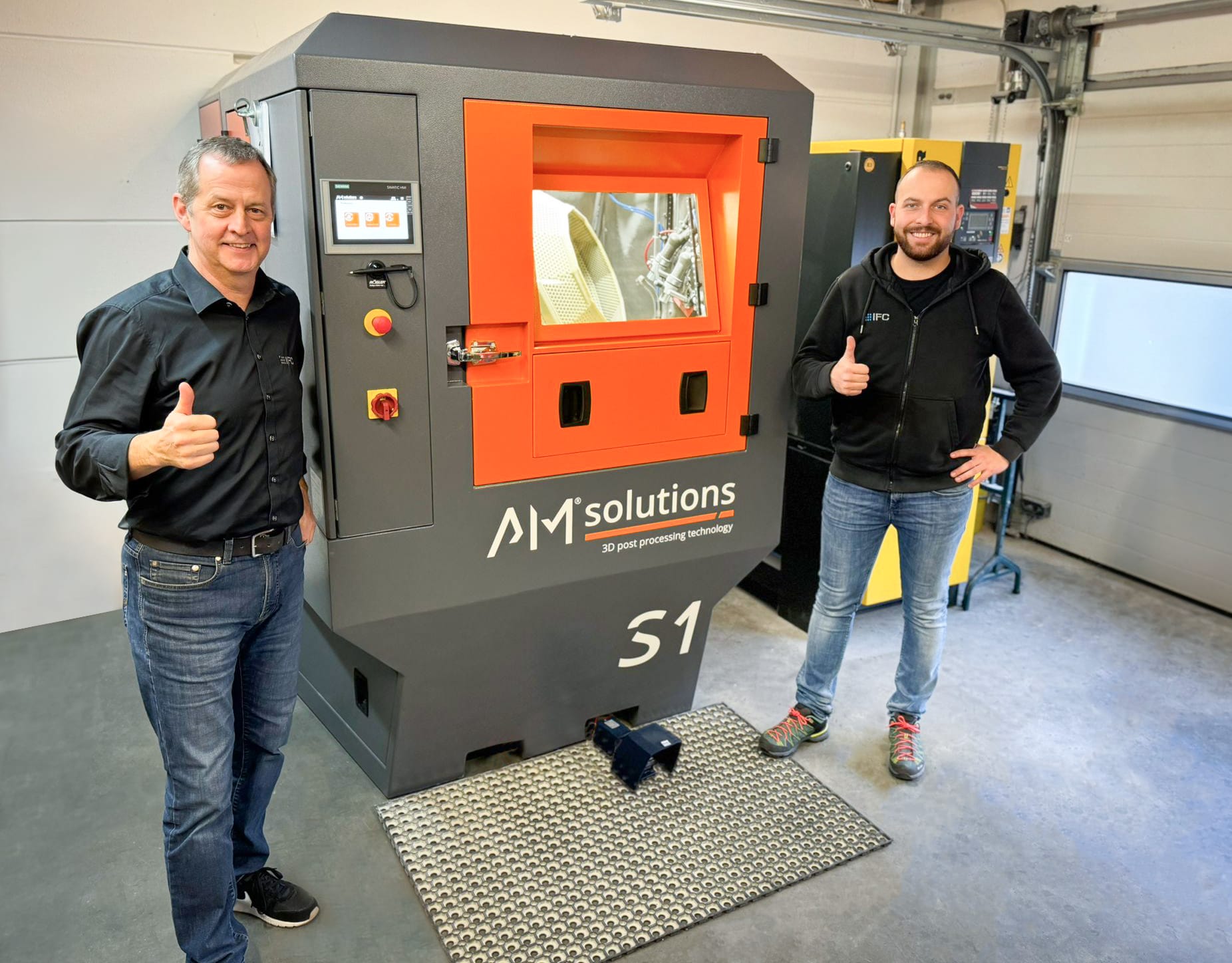
Dominik Riegg
“With manual blasting, the quality always differed. Now we have the guarantee that everything fits and at the same time we save up to 70 % on manpower,” explains Dominik Riegg, Head of Additive Manufacturing at IFC (pictured above).
For further information please go to: www.solutions-for-am.com
For over 80 years, the privately owned Rösler Oberflächentechnik GmbH has been actively engaged in the field of surface preparation and surface finishing. As global market leader, we offer a comprehensive portfolio of equipment, consumables and services around the mass finishing and shot blasting technologies for a wide spectrum of different industries. Our range of about 15,000 consumables, developed in our Customer Experience Centers and laboratories located all over the world, specifically serves our customers for resolving their individual finishing needs. Under the brand name AM Solutions, we offer numerous equipment solutions and services in the area of additive manufacturing/3D printing. Last-but-not-least, as our central training center the Rösler Academy offers practical, hands-on seminars to the subjects mass finishing, shot blasting and additive manufacturing. The Rösler group has a global network of 15 locations and approx. 150 sales agents.
For more information, please go to: www.rosler.com