~ Vibratory linear screens harness nutrients in kibble production lines ~
Around 160 million tonnes of seafood are harvested and processed each year globally, according to the American Chemical Society’s Turning Food Protein Waste into Sustainable Technologies study. Astonishingly, only 20 to 50 per cent of this vast quantity is recovered as edible food. The rest is classified as byproducts or waste — and rich in unused protein. Here, Stephen Harding, managing director at the material handling specialist Gough Engineering, explains how vibratory linear screens support pet food manufacturers in yielding protein’s benefits and harnessing waste sources of protein.
Like many byproducts of the meat industry, seafood waste is incredibly rich in collagen — one of the most abundant proteins in the body. Fish skin, scales, fins and bones are all rich sources of protein, which the American Chemical Society’s report describes as, “the most valuable of the macronutrients from both an economic and human diet perspective.”
A leading manufacturer of premium dry pet foods, based in the UK, sought to address how food protein waste was being handled in its production line. They needed a different approach: processing cold press and raw meat into an additive and incorporating this into its kibble. The result was a nutritionally rich pet food containing the right levels of protein content.
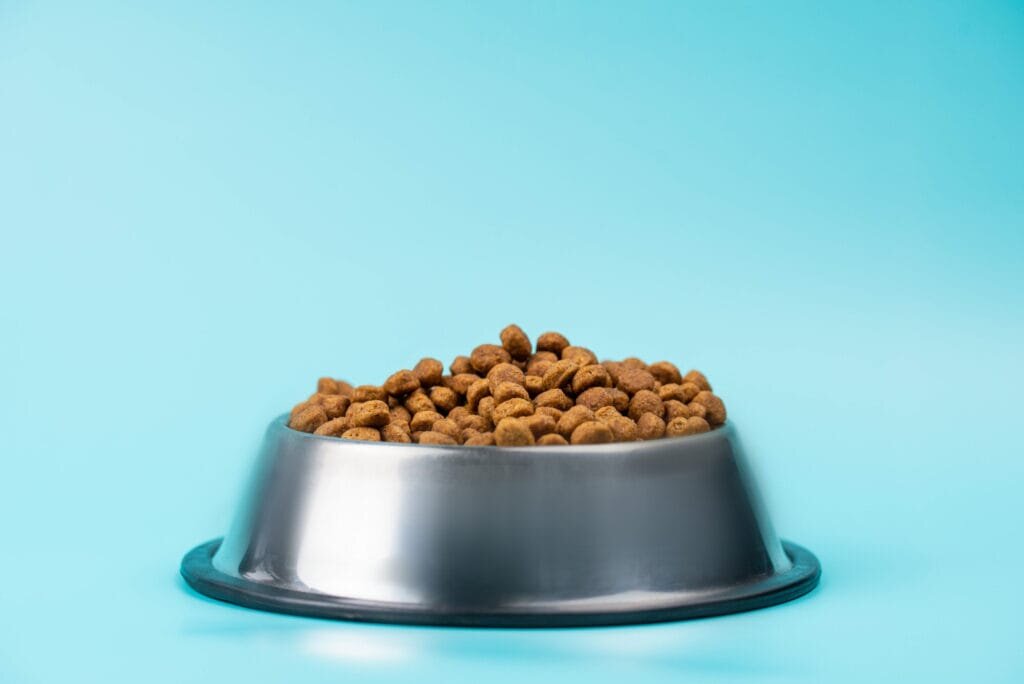
Nutritionally rich pet food must contain the right levels of protein content.
Extracting protein
To achieve this, the protein would be extracted through specialised processes. The screening of waste — containing residues from the bulk product — would then be recycled back into production in order to ‘close the loop’ on waste. This scheme underlined the manufacturer’s strong dedication to sustainable business practices.
However, the conscientious approach would necessitate quality control screening processes. It would also require feeding/conveying equipment provided by a material handling specialist.
The food manufacturer approached Gough Engineering. To support the customer with its new production requirements, Gough designed a scheme/system comprising various vibration screening, conveyors and feeding systems. Specifically, Gough’s offerings included linear screens for quality control screening and bucket elevator systems. The bucket elevators would gently handle and feed the product, by gravity from an elevated output, to the final bagging and packing processes.
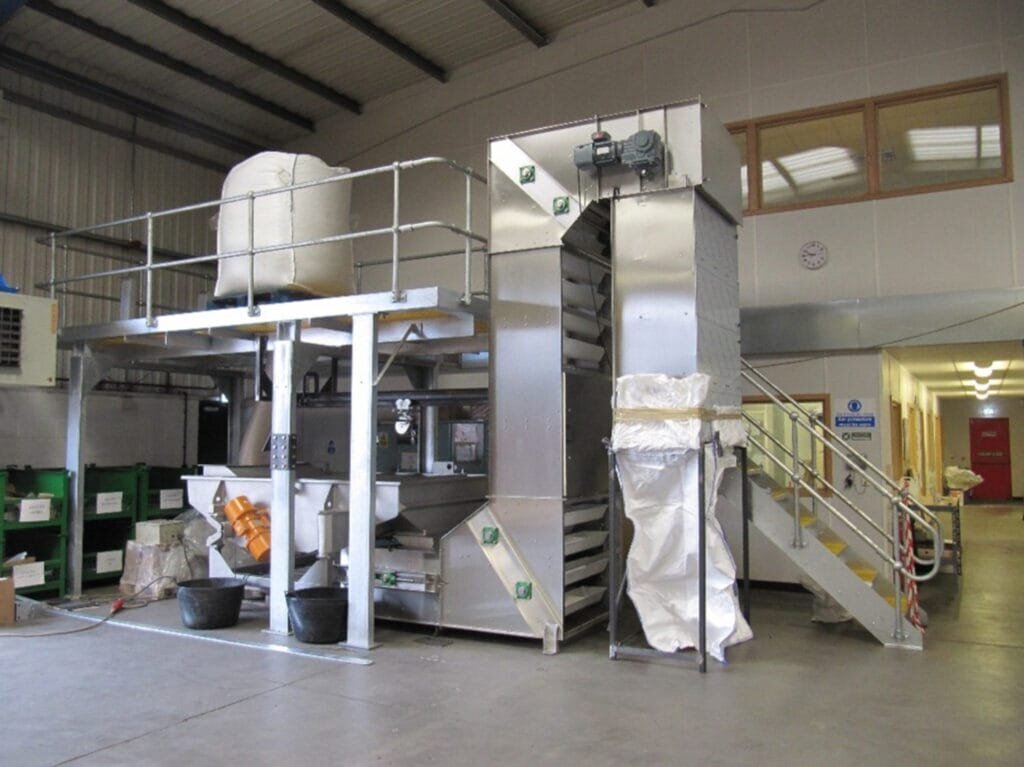
Gough Engineering’s gravity fed Z configured Swinglink® bucket elevator.
Vibratory linear screen
A comprehensive system was developed, incorporating a vibratory linear screen, a fines removal screw conveyor, gravity fed Z configured Swinglink® bucket elevator and supporting platforms. The equipment, designed for cleanliness, featured a combination of powder coated mild steel and stainless steel. Additional elements included roller stops, pneumatic slide valves and vibration isolation components — all aimed to deliver the desired quality product to the packing lines.
Crucial to the new system was a vibratory linear screen used to separate fine particles. The screen was equipped with twin side-mounted vibratory motors and Rosta Suspension Mounts and sized to the correct product throughput, designed to provide suitable separation.
The screen is designed to offer product screening and feeding in one system, increasing the quality and value of product through the screening of unwanted sizes. The vibratory linear screen would be essential to maintaining the kibble product prior to bagging, keeping it to the highest quality assured particle sizes. Additional options included screening meshes that could be replaced for cleaning and maintenance.
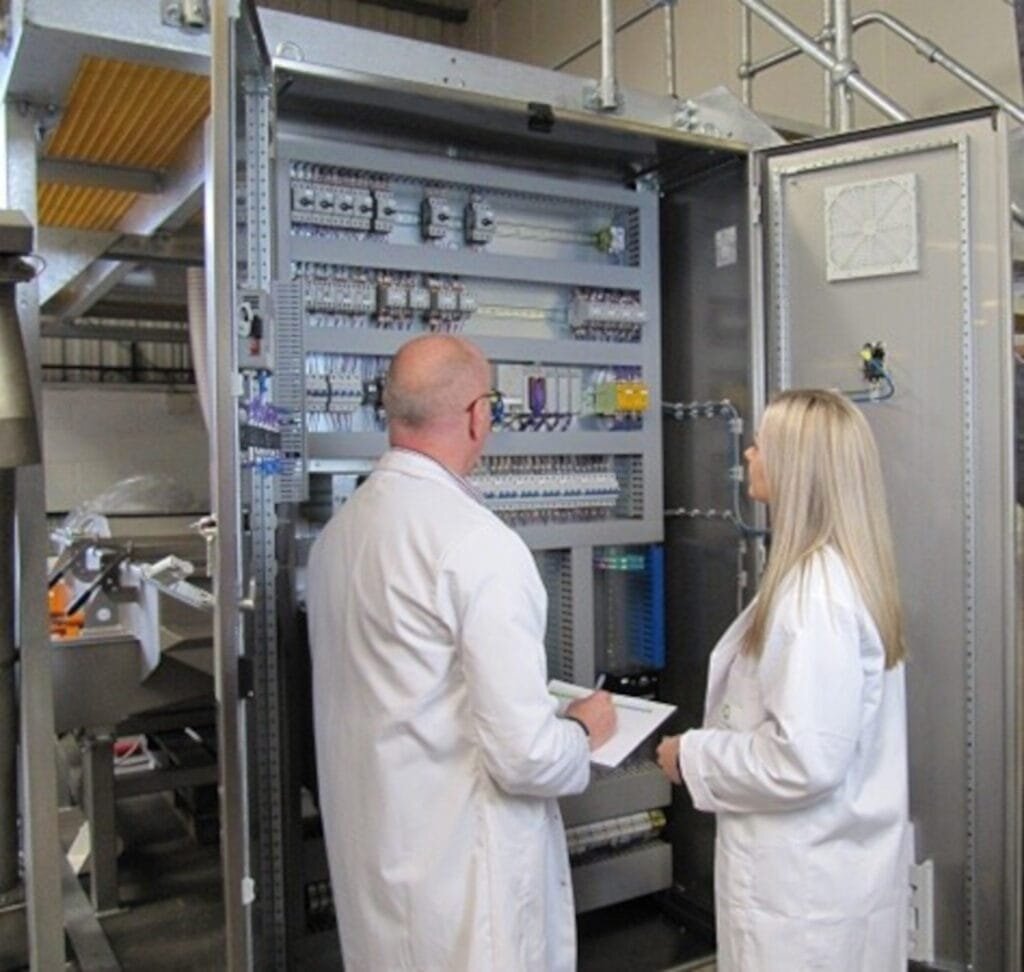
A leading UK manufacturer of premium dry pet foods sought to address how food protein waste was handled in its production line.
Designing the system
Gough’s design engineers worked closely with the customer to design the system to suit its unique requirements. Gough Engineering generated and submitted detailed engineering drawings. This was followed by manufacture, assembly and testing at its in-house factory to verify that the system aligned with the customer’s unique requirements.
The final step involved on-site installation and optimisation using SolidWorks and 3D concepts, guaranteeing a seamless fit within the company’s existing infrastructure. This customised approach allowed Gough to adapt its screens, conveyors, and feeding systems to precisely cater to the pet food manufacturer’s unique requirements.
With Gough Engineering’s tailored solutions in place, the customer achieved a notable throughput of around 17 tonnes per hour. The screens, conveyors, and feeding mechanisms integrated into the customer’s modern pet food production line. As the world grapples with the challenges of animal waste and associated environmental impacts, Gough Engineering’s support of the UK pet food manufacturer shows how conscious choices and strategic partnerships can help extract and combine protein’s benefits with dried pet foods.
To learn more about Gough Engineering’ vibratory sieving solutions for manufacturing pet foods, visit its website.