Ben Buchele Elektromotorenwerke GmbH has delivered two electric motors to Reintjes for installation on a hybrid dredger, called Chicago, at the Port of Hamburg, Germany.
The Nürnberg, Germany-based company manufactures standard and custom-built motors for shipbuilders and other heavy-duty applications globally. Reintjes is a specialist in maritime gearboxes and powertrains; in this instance it was contracted to provide a hybrid powertrain consisting of two diesel engines and two electric motors, helping the ship operate at low emissions when close to port.
The end user wanted an electric motor solution that enabled fully electric power at a speed of up to six knots, and offered the capacity to recharge the batteries, while using the diesel engines. Reintjes asked Ben Buchele for a weight-optimised, water-cooled engine that met certain criteria, such as 60 kW of power; frame size 200; rated speed of 2,130 rpm; inverter duty; and suitability for S1 continuous duty.
Detlef Koslowsky, head of sales at Ben Buchele, said: “Special calibration is required to allow a hybrid system to easily switch between drive modes. One way to change from electric operation to diesel power is by using the control lever. Moving the lever by a small amount manoeuvres the ship using electric power. Once the lever reaches a set position, the diesel engine kicks in. However, a simple button is another method of switching between modes—and was the solution implemented for the Chicago. If the lever is in neutral, the captain can select electric mode by pressing the button and continue to steer the ship using the control lever. Drive modes can be changed at any time, even when the ship is in motion and the propeller is turning.”
Louis Zander, director of sales and service at Reintjes Hamburg, said: “In order to deliver the various operating modes, the motor has to allow such high speeds and be able to draw its rated power across a broad speed map. We designed the motor to produce almost two times the rated speed. In other words, the motor was designed to run at up to 4,300 rpm in PTO [power take-off] mode, or when operating as a generator, but needed to supply 60 kW of power at as low as 2,000 rpm so that it could operate at full capacity at the required speed of six knots in electric mode. Only Ben Buchele motors can achieve this kind of map.”
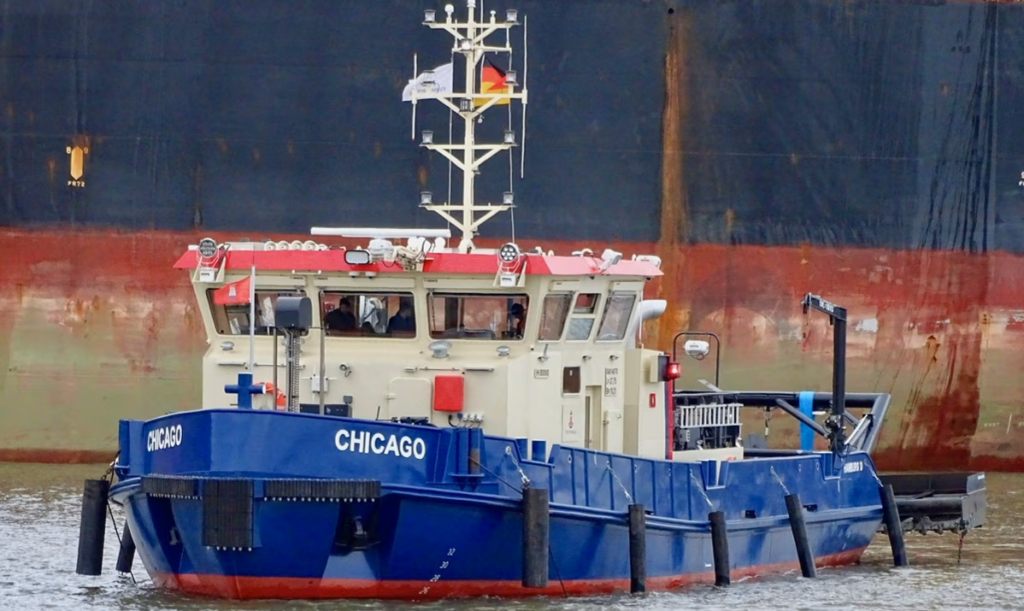
he dredger, Chicago, is a twin-engine vessel with two propellers and two prop shafts.
Twin-engine vessel
The dredger, Chicago, which shifts sediment in certain areas of the port so that it can be extracted by the suction dredgers, is a twin-engine vessel with two propellers and two prop shafts. Each prop shaft is powered primarily by a diesel engine, but also has an electric motor to enable low-emissions operation. Even when the ship is in electric mode, both propellers are still available, ensuring full manoeuvrability. This is made possible by the redundancy built into the system that allows a single prop shaft to be used if one of the propellers fails.
The water-cooled electric motors were favourable in the warm engine room environment. All of the power electronic components, from the batteries to the variable frequency drive, generate a certain amount of heat. Water-cooling the electric motors eliminates all further sources of heat. Another major advantage of a water-cooled motor is their low weight and compact size, meaning they can be installed without taking up too much space. Water-cooled motors output the same amount of power as a surface-cooled engine at a much larger frame size.
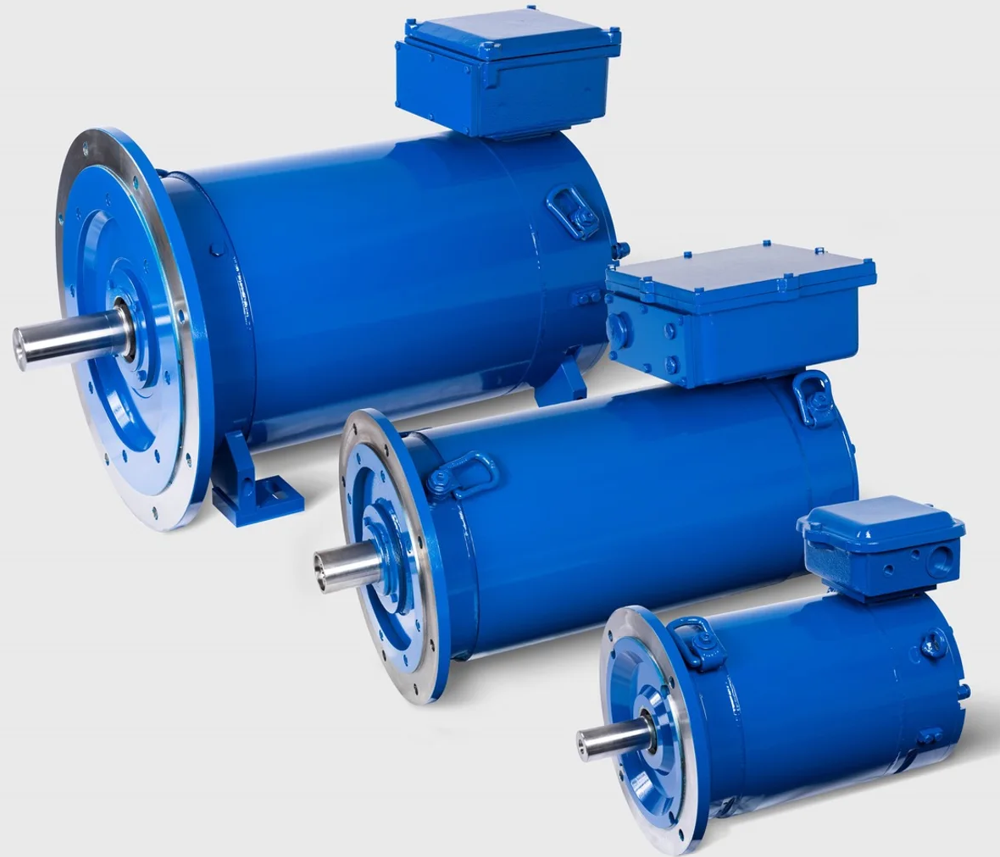
Ben Buchele’s water-cooled electric motors were favourable in the warm engine room environment.
Koslowsky also pointed to the flexible universal base, which allows the motors to be installed in a variety of locations on the ship, and the ability to adjust the position of the junction box depending on customer requirements. Normally, the box is located on the right-hand side of the motor, but Ben Buchele lets customers choose exactly where they want their terminals—and change their mind at any time up to the point of assembly.
Koslowsky added: “Hybrid drivetrains combining conventional diesel engines and high-tech electric motors were once unusual. Today, they offer genuine alternatives in the search for more sustainable drive solutions, as the shipping industry navigates the renewable transition.”
Reintjes’s overall solution incorporated the entire hybrid system, which includes the reversing gear; the electric motors; the flexible clutch between the electric motors and the transmission; the variable frequency drives that control the electric motors; as well as the ship control system, consisting of the control lever and cabinet.