Environmental matters continue to be of major focus in most European economies. Underpinning this trend is increasingly stringent legal obligations across the continent, many of which necessitate the submission of detailed environmental data. This requirement is likely to become even more challenging in the coming years. As a result, working with an environmentally responsible motion control solutions supplier such as NSK Europe is of paramount importance.
NSK Europe continues to make improvements to its environmental credentials, with the past 12 months seeing significant progress in a number of key metrics as the company works towards its ultimate carbon-neutral goal.
The business is well on track to meet its target of reducing Scope 1 and Scope 2 carbon emissions by 80% in the current financial year in comparison with the FY2017 baseline. Stand-out initiatives include the introduction of new gas-fired boilers at NSK Europe’s Kielce plant in Poland, replacing old coal-fired boilers. The company expects this investment to save up to 2,500 tonnes of carbon emissions per annum.
As a further example, NSK’s European Distribution Centre (EDC) in Tilburg, Netherlands, successfully negotiated a contract with its energy supplier to supply 100% certified ‘green’ electricity. This initiative will save 400 tonnes of annual carbon emissions. In fact, as all NSK Europe plants and warehouses are now purchasing green electricity, the company’s Scope 2 emissions are close to zero. This bodes well for subsequent targets: 90% reduction of Scope 1 and 2 emissions by 2026 (against FY2017); and 100% reduction (zero Scope 1 and 2 emissions) by 2030.
Of course, reducing carbon emissions is about far more than energy alone; attacking metrics such as water consumption and waste generation is also very important. Many initiatives at NSK Europe are currently underway to help the company deliver on its FY2023 target of reducing water consumption by 6% against the FY2017 baseline. The Kielce plant, for example, lowered its water usage by 500,000 litres a month by changing to a recirculating system for cooling the site’s remediation pumps.
Another plant implementing changes is Newark, UK. By installing the company’s first rainwater harvesting unit the site saved an estimated 200,000 litres of mains water in the first 12 months of operation. The harvested ‘grey’ water sees use in restroom toilet facilities.
NSK Europe is also targeting waste, already achieving a 16.5% reduction against the FY2022 baseline and accomplishing a recycling level of 96.8%. Reducing waste such as steel scrap, grinding swarf, used oil/emulsion and oil-contaminated waste is of significant benefit to the environment and saves on waste processing costs.
In the current financial year, NSK Europe is running several waste reduction initiatives. For instance: the NSK Needle Bearing Poland (NNBP) plant is now selling 1,000 kg of waste wooden pallets a month for recycling; the Kielce plant is taking advantage of reusable oil cleaning cloths to reduce this sort of waste by 22,500 kg per month; and the AKS Precision Ball Poland plant in Żarów is separating oil from emulsion waste to allow recycling and reduce monthly waste of this type by 1,000 kg.
Although improvements at manufacturing facilities have the greatest impact on sustainability, NSK Europe’s non-manufacturing resources are also playing their part. For instance, offices at the company’s Ratingen facility in Germany upgraded large sections of its lighting system to LED fittings, which use around 75% less energy. NSK Europe’s logistics function is also reporting progress, introducing a shredding machine to repurpose cardboard waste as protective infill instead of using plastic bubble wrap.
Despite the challenging business climate, NSK Europe continues to make environmental improvements set against tough CO2 reduction targets. Ultimately, the company is determined to help build a sustainable world by pursuing advanced environmental practices.
1) NSK’s first rainwater harvesting unit has saved the company’s Newark, UK premises 200,000 litres of mains water in its first 12 months of operation
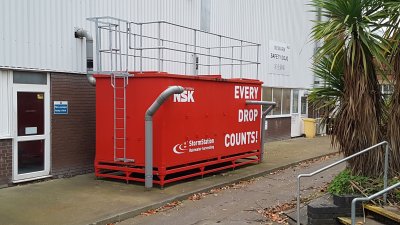